How to Write a Construction Accident Prevention Plan
Not every company has a construction accident prevention plan, even though falls are the leading cause of construction deaths. The Occupational Safety and Health Administration regularly emphasizes that all of them are preventable. The job site is where the majority of injuries and accidents occur, and where accident prevention must start. Safety regulations put in place by OSHA and other organizations help contractors and their workers avoid injuries and death. In order to prevent injuries on the job site, contractors must implement a construction accident prevention plan.
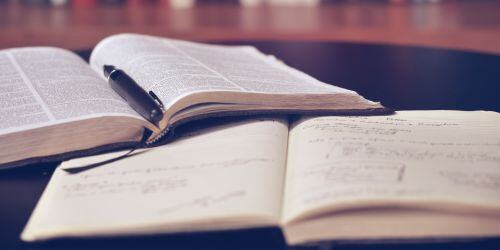
Table of Contents
Starting a Construction Accident Prevention Plan
First item to establish should be who is responsible for the creation and implementation of the construction accident prevention plan. They will be responsible for researching the best methods for avoiding injuries and comparing them with the current plan in place. They might be a safety coordinator or other such title, or someone else in the company who has time.
One of the best places to begin researching is the Occupational Safety and Health Administration’s website. They have information available for the latest on ergonomics for tools, as well as recommendations for every subcontracting field. It’s an easy place for the person creating the plan to see the standards and recommendation.
Another good place to look is through equipment use videos and guides. They usually have lists of guides or training to use equipment and tools. Manufacturers regularly publish guides on the appropriate way to use their tools and equipment, with some equipment needed special certification. Reading those guides and taking those training sessions can be a good way to increase awareness of safety.
Another great resource for developing a construction accident prevention plan is actually insurance companies. Insurance companies will often provide the safety coordinator with resources. Especially since they prefer people to not end up injured on a job site. The coordinator can use the insurance company’s resources to write and develop the accident prevention plan.
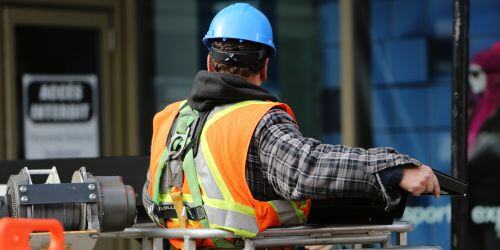
Creating the Accident Prevention Plan
Once all of the research is gathered, the safety coordinator, or designated person, can write the construction accident prevention plan. The accident prevention plan should cover a lot of ground, there must be sections on first aid and emergency medical response, drinking water, restrooms, scaffolding and other falling risks, and more.
The safety coordinator needs to write a first aid section. This section outlines the proper response if someone gets injured. Someone who knows how to administer first aid and CPR should be at each job site, in case they are needed. And it should have a sufficient number of kits for the number of workers available.
There should also be potable drinking water to prevent dehydration and other issues, and appropriate sanitary toilet facilities. This ensures that the workers won’t get sick from their water.
Every accident prevention plan should include a personal protective equipment section about which gear is necessary for the site. The safety coordinator should write an outline of how often workers should check their personal protective equipment and when it should be replaced. This is a document that all the field workers can sign to indicate they understand.
The safety coordinator must write a section covering the varying conditions on a job site and their hazards. For example, working over water, working at great heights, material storages, welding and cutting, and more specific working conditions and their accident prevention plan.
Finally, there should be a set of disciplinary rules for those that don’t abide by the accident prevention plan. While abiding by the safety rules is a benefit to workers, that doesn’t mean that everyone will follow the rules. However, with the right implementation plan, it should be easier to get all workers to follow the accident prevention plan.
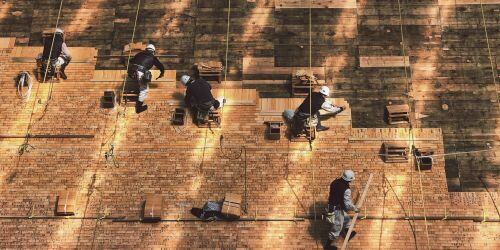
Implementing the Plan
Any new policy or plan has to come with the full weight of upper management. Once everyone knows they’re on board with the plan, and there are real consequences for not following it, it is easier to implement it. When upper management agrees to the plan and even discusses the importance of increased safety on the site, it leaves little room for other employees to not pay attention.
Once upper management is on board all employees must be trained on the construction accident prevention plan. Workers can use the meetings to ask questions about any new processes or even why or how the new policies will work. Workers can use the meetings to understand the rationale behind why and how the policies will work.
However, training doesn’t just happen once. There must be constant training to ensure that everyone is not only up-to-date with any changes to the plan, but that new hires have the opportunity to go over the plan. It’s also beneficial to go over the plan regularly so that it’s easily memorable. While follow up training sessions don’t have to be hours long, a quick safety standup at the beginning of the day can make a huge difference.
A construction accident prevention plan is crucial to be able to effectively manage potential hazards on the site. Construction can be a dangerous industry, that’s why it’s so important to ensure everyone is as safe as they can be.
FAQs for Writing a Construction Accident Prevention Plan
What makes a construction accident prevention plan essential for construction companies?
A construction accident prevention plan is crucial because it helps prevent injuries and accidents on job sites. Falls and other incidents are preventable, and having a well-structured plan in place is vital to ensure the safety of workers.
What are the initial steps to begin developing a construction accident prevention plan?
The first step is designating a responsible person, often a safety coordinator, to research, gather information, and create the plan. This person can start by researching safety standards and recommendations from organizations like OSHA and equipment manufacturers. Insurance companies can also provide valuable resources.
What are the key components that should be covered in a comprehensive accident prevention plan?
A well-rounded plan should include sections on first aid and emergency medical response, drinking water, restroom facilities, fall prevention, personal protective equipment (PPE) requirements, hazardous working conditions, and disciplinary rules for non-compliance.
What strategies can be employed to make sure that employees are aware of and adhere to the plan?
Implementing the plan effectively requires the support of upper management and clear consequences for non-compliance. Regular training sessions, including meetings for questions and discussions, help ensure that all workers understand and follow the plan. Ongoing training and safety standup sessions can reinforce safety measures.
What role does upper management play in the successful implementation of an accident prevention plan?
Upper management’s support and commitment to the plan are crucial. When they endorse and emphasize the importance of increased safety on the site, it reinforces the plan’s significance to all employees and minimizes resistance to safety measures.