5 Tips for Electrical Estimating and Costing Projects
Estimating and costing electrical projects is a crucial step in every construction project. Without electrical estimating, it is difficult for owners to accurately calculate total project costs. On the flip side, it is also hard for contractors and trade contractors to know how long a project will take or what materials are needed. It’s important to look at all processes in a business and see where they can be improved. Here are several tips to help improve electrical estimating for construction projects.
Table of Contents
What is Estimating
Construction companies are able to forecast overall project costs by using estimating. They carefully estimate the cost of the physical structure, overhead, and other costs associated with the business and project. Because estimating is such an important part of the bidding process, many subcontractors submit estimates for specific jobs on a site before breaking ground. An estimating mistake can cause a project to become unprofitable for contractors, which gives them high motivation to ensure accuracy when estimating. Additionally, without an estimate, both subcontractors and trade contractors can’t accurately bid on a project. Estimates must include the estimated cost of the project plus overhead and estimated change order and change data.
Why Electrical Contractors Need Estimating
Estimating is a crucial part of the construction process and no company or industry can avoid it. Without estimating, owners don’t know what it will cost for a project to be completed. Electrical contractors, in particular, need estimating because there are a lot of individual parts that must be ordered and installed. The costs of conduits, wiring, and more can fluctuate over the year, just like the cost of electricity and other office-related costs. Electrical contractors need estimating to ensure that all of their costs will be covered and they will be able to turn a profit on every project.
What Goes into Estimating and Costing for Electrical Projects
Estimators must consider several factors when estimating costs. Before estimators take on the time-consuming process of estimating a job, they typically use historical data to determine whether the job will be worth the time and effort needed to complete an estimate. If the crew doesn’t have the right or enough experience, then it usually isn’t worth it to submit a bid for the job. However, once estimators identify a job that will turn a profit for the company, they will use this information to build the estimates
Overhead
Estimators have to take the overhead costs into account when preparing estimates, as they are one of the most important costs to be incorporated into the bid. Overhead costs include all of the indirect costs of a job such as accounting fees, marketing, insurance, legal fees, rent, taxes, phone bills, utilities, and more. All projects must have overhead factored into them, otherwise, the business won’t be able to keep the lights on. Any good accountant should be able to help calculate what the overhead costs should be, however, it’s common practice for companies to do overhead as a percentage of estimated costs.
Takeoffs
Takeoffs, or take offs, are the estimated quantities of items that the electrical contractors need for a project. Using the plans or drawings, estimators determine the specific items and number of items that they need to order for the job. Depending on the tools and experience of the estimator, they have several ways to calculate the takeoffs.
Some estimators will do manual takeoffs from designs and drawings, while other estimators use estimating software to determine appropriate takeoffs for a given project. Takeoffs need to be as accurate as possible with the estimators erring on the side of caution, as not enough materials are ordered, and electrical contractors will have to submit a change order.
Labor Costs
Labor costs are the final piece of the electrical estimating process, and the size of a firm can determine what process estimators use for labor costing. For example, smaller firms will often use their experience in past jobs to determine the number of hours needed for current jobs. However, this method isn’t great for larger firms as it leaves more room for error and can be inaccurate. Many larger companies instead choose to determine labor costs by using labor units, which are set by how long it takes to install every component by the number of laborers.
Tips to Improve Electrical Estimating in Construction
Here are some of our top tips to help improve electrical estimating in construction projects.
1. Review Cost Codes
No two businesses will use the same cost codes. Companies might use just a few cost codes, or they might have hundreds of cost codes. More cost codes mean that the company can track items in detail, however, they can be complicated to function. Companies should review their cost codes to determine whether their cost codes are functional or not and if it’s making sense for the business.
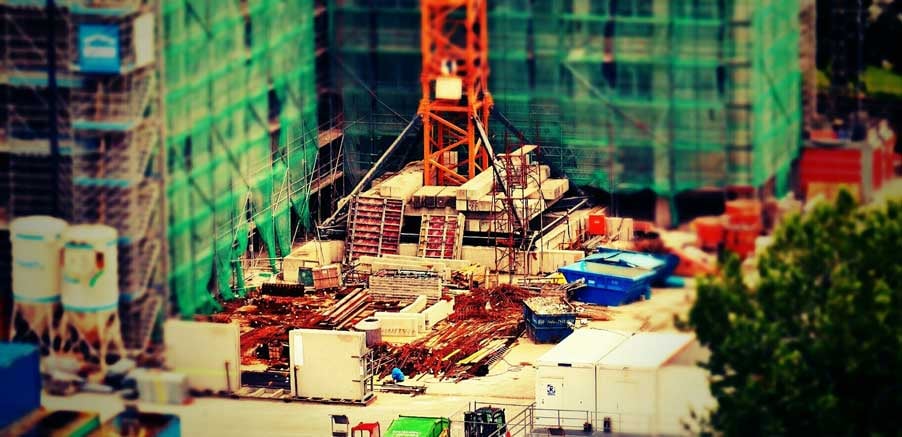
2. Carefully Determine Overhead
Overhead costs include all indirect costs incurred during the life of a project, such as utilities for the office and marketing costs. Accurately estimating overhead costs is extremely important, as an underestimated cost can lead to the project becoming unprofitable for the contractor and may even end up costing the contractor money.
3. Mobile Time Tracking
Mobile time tracking is an easy way to improve accuracy for estimating and costing electrical projects. Paper or manual time tracking doesn’t provide accurate information, and switching from manual to mobile time tracking helps improve labor cost estimation. It’s easier to know how much time a team needs to complete a specific cost code or certain projects. More accurate information leads to more accurate estimates, decreasing the number of budget overages by the end of the project.
4. Review Old Projects
One of the best ways to improve estimating is to look at old projects. Projects that are similar to the current bid can provide valuable data since an estimator might be able to see that similar projects always end up over budget on labor costs or material costs and account for that in their new project estimate. Historical data can also be used to determine the general overhead during certain times of the year and more. They can also use it as a way to validate their estimates. If past projects always use a certain labor amount, then using that data to validate the labor cost can be beneficial.
5. Determine if the Project is a Good Fit
While some projects may seem to be appealing for a contractor, it is important to take the skill set of the workers into account. Using new technology or materials that your workers are unfamiliar with may greatly slow down the progress of the project and If your workers are not comfortable in the specialized field of the project they are working in, it may not be worth investing your time and money in.
Conclusion
Estimating is a crucial part of the construction process as estimates are used to build bids and win work. However, estimators must use all available data to determine whether or not a project proposal fits their type of work, experience, and timeline. Without these determinators, estimators could bid on projects that they can’t win or projects that they might not be able to complete. Electrical estimating is especially important in construction projects because of the sheer number of parts and the time it can take.
Estimators can use historical data, past projects, and current project reports to better their estimates for similar projects. The best tip is to move to a mobile time solution. A mobile time solution is an easy way to get better labor data and labor cost data. It can also help estimators know how long workers typically charge a certain cost code. These tips can improve electrical estimating for construction projects, and help companies bring in more profit for the new quarter.
If you’re interested in using construction management software to improve your electrical estimating, and more, schedule a demo to learn how eSUB can help.