The Subcontractors Electrical Change Orders Guide
Electrical change orders are an essential element of any construction project and electrical construction is no different. Each contractor is going to process their electrical contractor change order form in a different way, though. This can lead to issues. When you need to adapt to a shift in the middle of a project, how well you act and document it can wildly impact client satisfaction and relationships with your fellow contractors. Here’s a full guide on how to properly document change orders for the benefit of your business.
Table of Contents
What are Electrical Change Orders?
In construction, a change order happens when the client or contractor wants a change to be made that strays from the original contracted plan for the construction project. For example, let’s say that an electrical contractor originally agreed to wire a set amount of rooms for an office building, but the client decided they needed more rooms.
This is not something that can be simply tacked on to the order. Before construction begins; contractors, architects, and project owners work together to document the plan and budget for the development process officially. Change orders are designed to make sure that the request is formally documented, and that the owner is held responsible for any sort of desired changes.
This means that the stakes are high with electrical change orders. Any order forms that are made need to be properly handled with caution as well as close detail. Any electrical contractors understand how frustrating it can be to work with a client that wants to change gears after work is underway. No party really benefits here. This is why it’s important to stick closely to the contract to avoid clients who may try to take advantage of contractors or pressure you into doing extra work without the extra pay. Change orders need to be firm in what extra work is going to be done and how much extra it will cost.
So, where are some of the common areas that companies go wrong with their change orders?
No formal process: This hurts in multiple ways. Not only does it take longer to draft electrical change orders, but it becomes harder to create a standard in regards to what changes are feasible and acceptable.
Bad communication: No contractor wants to be taken advantage of. Be sure you communicate your expectations to a client to make sure everyone fully understands what’s feasible.
Not preparing for the worst: Clients that were pleasant can switch gears when it comes to money. Make sure you have a worst-case-scenario plan if this issue enters the legal arena.
Avoiding Conflict With Electrical Change Orders
As one can imagine, things are rarely smooth when a change order is put in. The most frequently disputed area in the change order process for electrical subcontractors is the cost of requested changes. Deviating from the plan is always going to mean more money needs to be spent, and in some cases, the contractor needs to be ready to explain exactly how.
Electrical change orders can be broken down into three cost categories; direct costs, indirect costs, and significant costs.
- -Direct costs: These include things such as direct labor, additional materials, equipment costs, job costs, and other expenses required to process and execute the change order.
- -Indirect costs: These generally entail additional overhead expenses and profit percentages.
- -Significant costs: These generally include the impact that comes with lost productivity, project delays, and other added costs.
Be sure to document these in separate categories in order to find the proper subtotal in each set. This will give your client the clearest picture possible of what these costs represent and why.
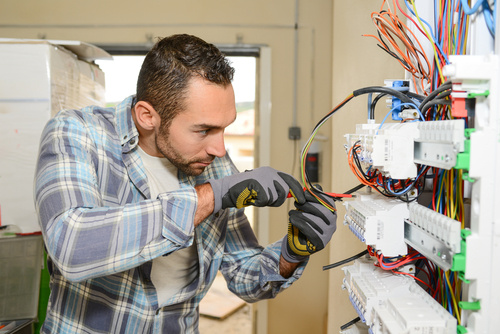
Change orders can cause disputes between contractors, subcontractors, and clients alike. While all parties want the best result, they are also looking for their best interest. As a result, conflict mediation plans are essential to avoid problems and resentment. Here are a few steps you can take.
Steps:
- -Arrange a meeting with owners, electrical contractors, and relevant subcontractors to discuss change orders before they are formally drafted.
- -Establish a strict policy for your company on how you handle change orders and apply them to every project. This ensures that no one project receives more of an advantage than another on change orders.
- -Keep reviewing and revising documents during the construction of a project so that every official document is accurate.
- -Establish accountability for every party involved when creating a contract for the project.
- -Communicate as clearly as possible when it comes to deliverables and expectations. Encourage other parties to do so throughout the course of the project as well.
A little bit of empathy goes a long way, but don’t feel that you need to be a doormat in terms of how you interact with your clients. If you layout costs for a client and they balk at them, you should stand firm when it comes to the added costs with a change order.
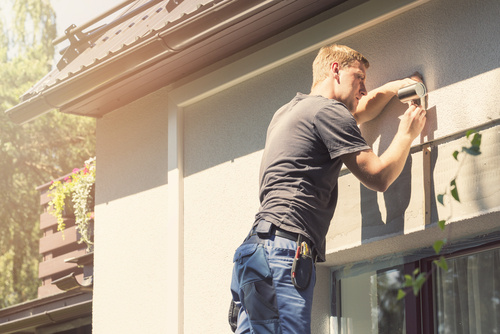
Struggling with the best way to manage electrical contractor change orders? While the process has an inherent frustration factor to it, it’s essential that you document it properly in order to ensure your business security and client relationships. In some cases, it’s the tools you are using to manage your electric change orders that are causing problems. Any sort of paper organization is extremely outdated and flawed. In some cases, even if you’ve digitized, you may be working with legacy systems that reduce your efficiency and security.
As a result, along with using tools like an electrical change order template, you should also be looking to implement project management software like eSub. Our cloud storage solution instantly provides a more efficient and effective method for you to go about storing your change orders. In addition, we provide additional analytics and tracking to make the contents of your orders more accurate and useful.