What are Building Specifications in Construction?
In the construction industry, every project needs specifications that outline all the requirements for completion. Such detailed instructions are written beforehand to describe how different construction aspects must be handled for the project. This can include materials, standards, quality, labor, skills, equipment, etc.
Building specifications must always be clear about how each construction activity must be completed. Think of it as a roadmap for the planning team. Not only does it bring everyone on the same page, but accurate construction specifications also help mitigate risks during the project’s lifecycle. The more complex a project, the more reliance on its specifications.
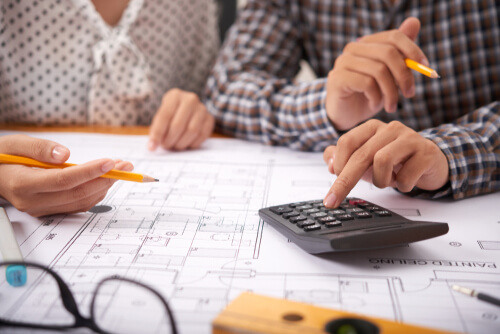
Table of Contents
Why Are Building Specifications Important?
Building Specifications (also called “specs”) are used by subcontractors and teams as guidelines for choosing the right materials for a specialized project. Their overall purpose is to define the requirements for project execution regarding installation, materials, products, procedures, and quality aspects.
The specifics that the owner and contractor discuss become the legal documents for the project and a keystone for the project design. The project is more likely to be correctly executed when the description and information are more precise.
Specifications can be categorized similarly to data because as project complexity increases, access to data is critical to making the right decisions. Additionally, a contract that precisely states building specifications considerably reduces risk during the project’s lifecycle.
Who Handles Building Specifications?
All building specifications are handled by qualified architects and designers alongside project engineers. The designing phase takes place before construction starts to ensure an accurate roadmap. Having building specifications outlined beforehand helps the construction project manager properly execute the design plan for every construction phase.
Large-scale construction projects are fairly more complicated. Hence, the design process reduces project risks and gives project managers a detailed outlook to meet deadlines within budget.
Do note that while building specifications are separate from building designs and construction drawings, all necessary details should be updated as plans get more complicated.
Types of Construction Specifications
In every construction project, three types of construction specifications help lay out the workflow: Performance, Prescriptive, and Proprietary.
1. Performance Specifications
A performance specification specifies the operation of a project. They also tell the contractor what the final installed product is capable of accomplishing.
Performance specifications focus on the project outcome and how it functions. Architects will give direction to the general contractor on what is necessary for the project.
Then, the general contractor must determine the plan to achieve the final result. This approach gives flexibility and creativity in construction plans by limiting the architect’s or engineer’s extent of authority for the project.
2. Prescriptive Specifications
Different from determining the project plan, prescriptive specifications list the materials the contractor must use and the installation process. This approach falls more on the architect and engineer unlike the general contractor because of their knowledge and to ensure proper installation.
Typically, prescriptive specs have three key components:
- General – consists of design requirements, national quality standards, product handling, & quality control.
- Products – incorporates the different products needed for each task & the performance level for each product.
- Execution – overview of how to prepare & install materials & to test the quality after the project’s installation.
3. Proprietary Specifications
Some construction projects may specify that only certain equipment or materials be used for completion. This is often the case in renovation projects where equipment and installations are already available onsite. The given construction specs will note what equipment and materials from the site must be used for a specific activity or construction phase.
Architects and engineers avoid using this type of building specification unless it is imperative. This allows the contractor to pick and choose from a list of approved suppliers.
Using one specific product type can influence the perception of nepotism towards a particular manufacturer and may increase product cost because of the elimination of competitors in the bid phase.
Tips to Improve Building Specifications
The design and planning phase is crucial to the success of the project’s development. The construction industry is introduced with technology innovations like BIM, which provides companies with an explicit depiction of what needs to be done before construction and ultimately increases the importance of specs. The following are a few ways that can help improve your construction specifications.
- The purpose of construction specifications is to reduce risk during the project’s lifecycle. Hence, the design phase needs to be comprehensive. Try to be as detailed as possible while covering all aspects of the project such as materials, quality standards, construction methods, equipment, testing requirements, etc.
- Since multiple project stakeholders are involved, make sure that construction specifications are written in a friendly and easy-to-understand manner. Try to avoid using overly complicated terms or technical jargon.
- Within the same vein, building specifications should always be written by the same writer. This ensures that the documents have consistent formatting and terminology through to the end. If multiple writers are involved, make sure to keep the specs easier to navigate between different construction phases.
- It is often that a construction project may reference other projects. It is important in such cases to ensure that all building specifications are clearly aligned with requirements. There should be no confusion or conflicts between the project and its references when construction begins.
- Using construction management software with tools for documentation and submittals can assist a project in running more efficiently and effectively.
How Are Construction Specifications Different From Blueprints?
Both construction specifications and blueprints are important documents that are drawn up before the project’s construction. They are similar in that both provide a roadmap for construction, but serve entirely different purposes beyond that.
The best way to explain their differences would be by taking an example. Imagine a construction project manager hired to create a multi-floor basement. The blueprint will show how long, wide, and deep the excavation should be. The construction specifications, however, will go in-depth to highlight how to complete each activity such as how to dig the foundation, what equipment and machinery to use, what type of crushed gravel to use, the thickness of the lean, the number of steel bars required, etc.
In summary, blueprints provide a visual overview with details necessary to complete the project as a whole. On the other hand, construction specifications show greater detail and instructions for specific areas while explaining how to execute and complete their construction phases.
Conclusion
Despite being tedious and time-consuming, building specifications play a critical role in the construction industry. They are essential to the successful completion of each project.
Having a group of architects, contractors, designers, and engineers define all the building standards based on scope and requirements is the key starting point in every project’s lifecycle. It determines how a planning team can stay within budget while completing all activities to meet deadlines. This also ensures that all risks such as delays and mismanaged materials are mitigated to a considerable degree.
Be precise and accurate when drawing up specs because your team will use them to carry out each task.