What’s Construction Cost Control? 7 Tips to Improve It
The global construction industry continues to face challenges that impact the financial budgeting and profits of new and upcoming projects. Rising costs due to inflation, unsteady supply chains, and labor shortages are only some factors that are making it difficult for specialty contractors to maximize their profits. Considering that contractors reportedly paid around $97 billion more in materials and labor than expected in 2023, it has become more important than ever to accurately forecast cost estimates before starting a construction project in 2024.
There are several aspects to construction cost control, all of which help project managers avoid cost overruns by providing guidelines for estimates and forecasts of labor, material, and overhead costs. The purpose of a cost control plan is to help ensure the project is delivered on time, within scope, and on budget. The following article looks to help you improve your construction cost control methods by providing some valuable tips.
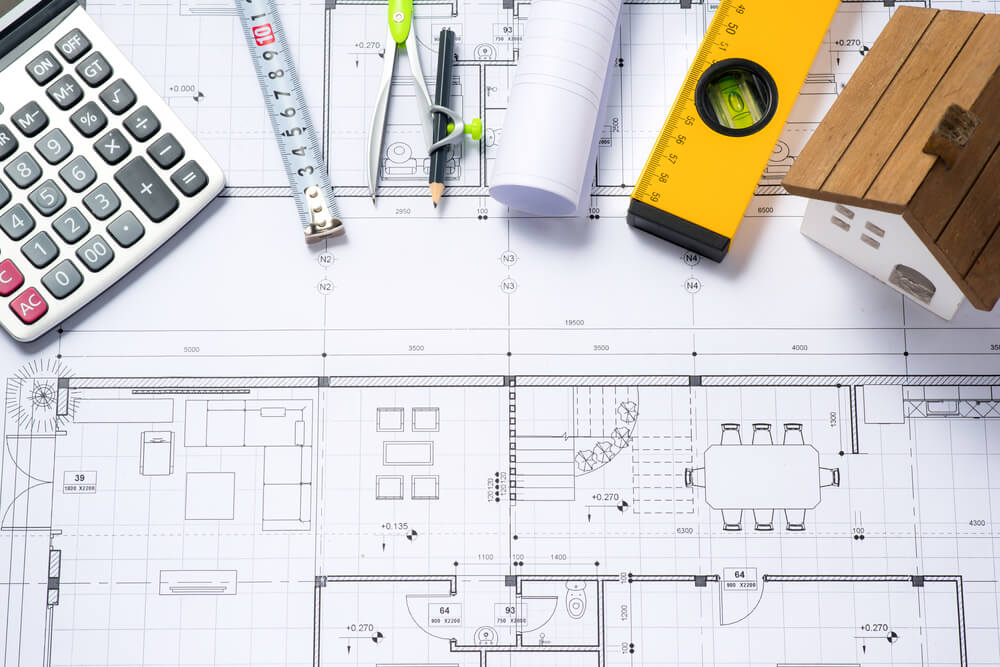
Table of Contents
How Cost Control Works in Construction
It all starts with preliminary budgeting where the contractor collaborates with stakeholders and the planning team to develop a detailed cost estimate based on the project scope, goals, and budget constraints. This covers all financing aspects such as the cost of materials, labor, equipment, risk mitigation, rental fees, etc, which can be tricky because of regular price changes in the market.
For example, a cost estimate might fit a high-quality material within budget. However, if that cost estimate doubles in the market in the months to come, it might no longer be feasible to use that high-quality material. The contractor will then have to either get another material type approved by the client or make adjustments elsewhere to balance out the budget constraints.
Accounting for time and varying market trends such as inflation in your construction cost estimates is, hence, extremely important. Delayed projects end up costing a lot more, which stretches your budget and eats up your forecasted profits. It is advised that building owners hire a construction manager with expertise and a good track record in construction cost estimation.
Tips to Improve Construction Cost Control Process
Basing a construction project on an inaccurate cost estimate analysis will mostly always force the project to overrun its budget. This will put the construction manager, contractor, and stakeholders in a financially tight spot where cost-cutting or cost-balancing decisions must be made to meet deadlines.
By regularly monitoring costs incurred and having a plan in place, proper cost control can help optimize the construction budget to safeguard your profits. Hence, construction managers must be well-versed in not only developing accurate cost estimates at the start but also overseeing varying trends outside of the project site to update the cost estimate analysis as quickly and efficiently as possible.
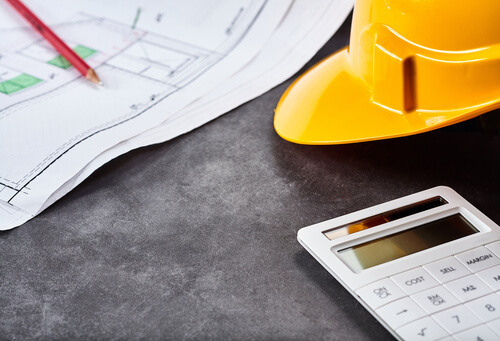
1. Use Construction Management Software
Using construction management software with data management capabilities helps update everyone on the job site on any changes to the project’s scope, which happens pretty frequently. It also helps connect back-office staff with workers on the job site to ensure an active line of communication across everyone involved in the project.
Mobile-based construction management software is also the perfect solution for the highly mobile workforce of varied skilled experts. From subcontractors to architects, each person can access one central system to see project plans and determine if it is necessary to adjust the construction cost control plan.
For example, if a drywall subcontractor needs to push back a wall and determines it will require extra time or materials, they can instantly upload that request on the software. Inputting this information would make all workers on the job site immediately aware of the changes to the scope and ensure there are no miscommunications that lead to delays or budget overruns.
2. Regularly Update Cost Plan
Consistently analyze and reevaluate cost plans to determine if it is necessary to make any alterations. If costs are higher than expected in one aspect of the process, balance it out by reducing costs in another area.
Remember that costs can be altered because of outside forces as well. External factors such as inflation or a shortage of materials can cause prices to change. Hence, a project that may have been within budget could now be over budget.
Another benefit of having construction management software is its capability to deliver real-time data on labor productivity and cost. This lets stakeholders make smart decisions at any point in the project’s lifecycle.
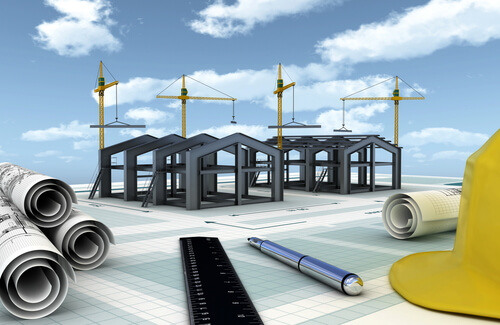
3. Consistently Submit Cost Reports
Ensure that you are providing cost reports to the client regularly. This helps keep them informed (and satisfied) with the on-site progress. Doing this also enables you to check the cost report against the construction cost control plan to determine the financial health of the project.
Cost reports are essential to streamline communication between owners, general contractors, and subcontractors. Updating management with real-time progress reports such as construction daily reports, helps identify early on if any delays or unplanned budget overruns may occur.
4. Prepare and Review Contingency Plans
By having set risk management procedures, project managers can plan for delays and budget overruns and have a plan of action on how to remedy the issues ahead of time.
Contingency plans help prevent having to pay premiums to get the project done on time when something goes wrong at the last minute. For example, construction management software can provide statuses of important submittals, RFIs, Change Orders, etc, which can warn if a project has a bottleneck and unexpected major delay about to occur.
Note that contingency plans are based on an evaluation of possible risks. They are not intended to cover changes to the scope of a project based on changing opinions or specifications.
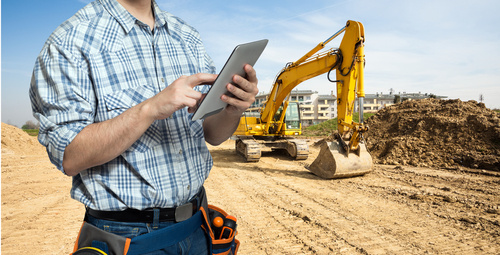
5. Encourage the Project Team to Design Within the Cost Plan at all Stages
Make sure you are following design development control procedures. For example, there is a general rule that 80 percent of the cost is determined by design and 20 percent by construction.
Additionally, make all team members aware that no team member has the authority to increase the cost of the work without balancing it out in another area.
Lastly, ensure each worker understands that construction plans are created per the total budget, and making changes could result in unplanned costs that exceed the projected budget.
6. Leverage AI for Better Forecasting of Construction Budget
Modern-day construction managers can gain a massive edge over competitors by utilizing artificial intelligence (AI) in their projects. There are several AI-driven construction software and tools available in the market that can create highly accurate cost control forecasts.
Their biggest advantage, though, is reading (and understanding) numerous data sets from various sources, which would be nearly impossible for a person who is already on the clock to do on their own. In addition, machine learning can offer deep insights that can help make informed decisions to control construction costs on the fly.
7. Set the Right KPIs
Key Performance Indicators (KPIs) provide valuable insights that allow construction managers to optimize and improve their measures of cost control while improving and increasing the overall performance and profitability of the construction team.
Tracking construction KPIs lets contractors keep tabs on how well their business is faring. This becomes a long-term relationship by providing regular benchmarks for project goals.
Some common construction KPIs for cost estimates can be cost variance, cost performance index, schedule accuracy, labor productivity, risk management, quality assessment, etc.
Use eSUB to Control Costs in Construction
It should be understood by now that construction cost control has evolved over the years with several complications for project managers to overcome. Hence, leveraging construction management software such as eSUB is the way forward. It not only helps connect all subcontractors, workers, and stakeholders on a single platform but also provides access to field apps and data sets to improve productivity for everyone involved.
The cloud-based project management software can, furthermore, be tailored to your specific needs, ensuring an optimized handling of your construction activities to control costs.
Consider scheduling a demo today and let us show you how we can help deliver your project in the most cost-effective way.