How to Set Operational Efficiency Goals for Your Construction Projects
Table of Contents
How to Set Operational Efficiency Goals for Your Construction Projects
Construction companies that work towards operational efficiency find ways to deliver goods and services in a cost effective manner without sacrificing quality. Obviously, an operational efficiency goal for all construction projects is to deliver the project on time and within budget. Because the scope of construction projects is so large, there are many ways to achieve operational efficiency. Breaking down operational efficiency goals for construction projects down into smaller categories—such as communication, safety, labor productivity, and customer satisfaction—aligns with the general thinking of “starting small to win big.” Executing on a smaller level increases the likelihood of success that will motivate your team towards achieving your larger operational efficiency goals.
Establishing the Benchmarks
To set operational efficiency goals of where you want to be, it is important to establish a benchmark of where you currently stand. Take a close look at your current processes and analyze them in detail.
-
How long does it take to process time cards—from employee entry to payroll?
-
What were the causes of your common injuries from last projects?
-
What is the time lag on project managers receiving information from the field?
This is a great opportunity for you to determine the pains in your processes. This is the start of determining the places for improvement and setting your operational efficiency goals. Below are some small places to start in order to make big operational improvements.
Operational Efficiency Goal #1: Breaking Down Communication Barriers
Those that have lived through a long-distance relationship know that communication is key to its success. The same exists for the relationship between the field team and the office team. Having an open line of communication between the field and the office will lead to improved operational efficiency. Daily reports serve as that important source of information to bridge the gap between the field and the office.
A simple operational efficiency goal to improve communication would be to complete a daily report before leaving the jobsite or within two hours. At a minimum, the daily report should include a photo of the jobsite at the beginning of the day and one at the end of the day. When this information is uploaded to a cloud-based construction project management system, the project manager can instantly view it and take any action as needed. Information captured from the field, such as jobsite issues, drawing questions, or delays, allows the project managers in the office to begin the documentation process immediately. This can improve the time it takes to document, communicate, and resolve issues. With this instant communication of jobsite activity or issues, the team works in tandem to clear up issues and move the project forward.
Operational Efficiency Goal #2 – Promoting Safe Behaviors
Construction is an inherently risky profession, and the job sites are dangerous. When one of your workers suffers an injury, a key piece of your team is missing. This can hinder your progress on a project. While every construction company strives for a zero injury goal, that is as unrealistic and unattainable goal. Operational efficiency goals concerning safety should be broken down into more reasonable goals. Setting goals around safety behaviors, such as X% of PPE compliance, modifications to correct safety problems will be made within X days, promotes healthy workers who are ready to move projects forward.
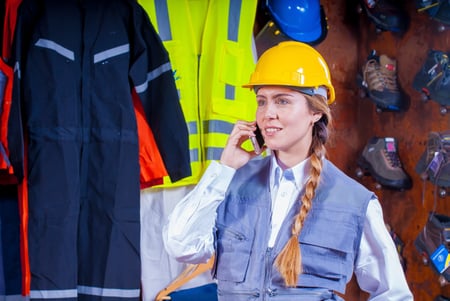
Operational Efficiency Goal #3: Improving Labor Productivity
Improving labor productivity can lead to higher profitability on projects. When developing proposals for jobs, the cost is based on the estimate of labor hours needed to complete the job. If fewer hours are used to complete the job, the subcontractors can pocket those profits. However, if more hours are used, the subcontractor may not be able to recoup those losses. The workers will still need to get paid for their work completed.
Tracking time towards job costing system will provide a granular level of detail of time utilization throughout a project. Tracking employee hours through the different phases of building and according to tasks on the job allows management team insight into the bottlenecks. Which tasks were taking longer to complete than anticipated? Why did the same task take longer in one phase than in the other? Are some crews or workers performing at a higher level than others? Tracking productivity through an integrated time and labor delivery system allows teams to meet its operational efficiency goals.
Operational Efficiency Goal #4: Ensuring Client Satisfaction
While a subcontractor receives awards due to a competitive bid process, a large majority of their business revolves around repeat business. Successful subcontracting companies deliver high-quality work that enables them to work with past customers and increase business opportunities through referrals.
According to Bain & Company, a 5% increase in customer retention can increase profitability by 75% because return customers will purchase more over time. A Net Promoter Score (NPS) measures the loyalty of a company’s customer base. The following questions will provide quantitative and qualitative view regarding your company’s customer satisfaction:
-
Quantitative: On a scale of 1-10, how likely is it that you would recommend our company to a friend or colleague.
-
Qualitative: Please tell us why you gave us that score.
An NPS score is based on comparing a company’s detractors and promoters. The score can be as low as -100 (all detractors) to as high as +100 (all promoters). In the business to business market, an NPS score between 25-33 is average. Rather than comparing yourself to other companies, it is beneficial to track NPS over time and establish operational efficiency goals around improvement. The comments provided by customers will determine the steps you need to take to improve those scores. In essence, those will also shed insight in how to deliver projects better.
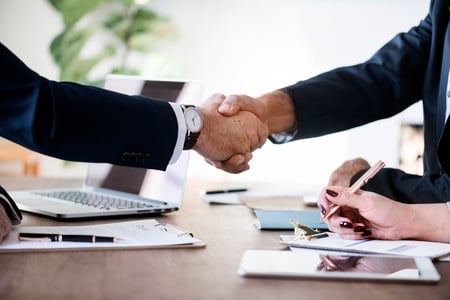
Implementing Project Management Software to Drive Operational Efficiency
Your team has done the hard work of setting operational efficiency goals. How do you get there? Construction project management software allows your team to track activities and communication around construction projects in a centralized location. It will enable your team to improve communication, promote safe behavior and track labor productivity to deliver projects in the most cost effective manner. If you can do all that, your customer will be happy and reward you with repeat business.
How eSUB Can Help
eSUB is a cloud-based project management platform built especially for subcontractors. It seamlessly integrates with leading construction software systems so you can easily switch from your current RFI process to a cloud-based system to upgrade RFI process.
eSUB organizes all of your project information in one place, allows for smooth collaboration, and streamlines communication through its intuitive interface. It also works on your mobile, so you can track projects on the go—no matter where or when—and stay up-to-date.