Covid-19: Mechanical Contractor Trends
eSUB’s mission is to empower trade contractors, and an essential part of that is coming together and sharing each other’s experiences. In the webinar, COVID-19 Facts from the Front Lines, hosted by Jeff Sample, we learn of mechanical contractor trends during COVID-19 from contractors themselves. Jeff is joined by mechanical contractors: Andru Coren and Ryan Hoggat. Andru Coren is the CEO and President of Eaglestone LLC and is located in New York, one of the largest hotspots for Covid-19. Ryan Hoggat is the Director of Manufacturing at University Mechanical Contractors (UMC). He is located in Seattle, another area that was primarily affected by the virus in its early stages. Both of the guests share their experiences and steps that they took after the initial shelter in place order and gave their perspective as mechanical contractors on the current times.
Table of Contents
Personal Protective Equipment
One of the first significant topics of discussion was about PPE (personal protective equipment) supplies and how long they anticipate having to use this protective equipment. Andru spoke about his experience trying to find the proper protective supplies and was fortunate enough to find and source a great bit of it. Being in New York, which is a major hub for supplies and goods helped tremendously. Andru emphasized that as a mechanical contractor, his most valuable asset is his workers, and so it essential to protect his people. When everyone goes back to work, we will still be in need of wearing this protective gear. It is wise to get the proper equipment now, as we are in this for the long haul.
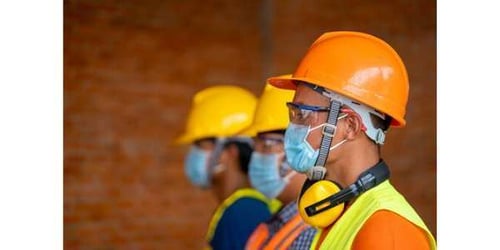
Delayed Supply Chain
The next area of discussion of mechanical contractor trends was about Ryan’s production of portable handwashing stations. He described how he was able to gather all of the materials for these stations. Ryan reached out to suppliers ahead of time and bought materials in bulk. His advice is to find multiple vendors when it comes to supplies, because everyone is going to be using the same vendors. If all of the demand goes to one vendor, supplies will get backed up and delayed. Having multiple vendors on deck is helpful to spread out the demand to different vendors. It is critical to have alternatives so you can be prepared and get the supplies you need.
Expectations
Many of the attendees were asking about expectations for when workers can go back to work. Andru made the point to keep your workers feeling as safe as possible when they do eventually go back to work. On the front lines, many workers do not want to go into work and risk getting infected. It is vital to have those safety precautions discussed earlier, as well as portable handwashing stations.
Jeff chimed in and spoke about leadership in these times. It is the leader’s responsibility to understand that many people are afraid, and mental health is as vital as ever in a time like this. When going back to work, keep these fears and feelings in mind when interacting with other people.
Following that, Ryan brought up a great point about prefabrication as well. He said that when we do go back onto the job site, there won’t be trade stacking. He recommends looking into increasing prefabrication opportunities to get as much work done offsite as possible. Prefab will help to maintain safe work environments and keeping a safe distance between workers onsite.
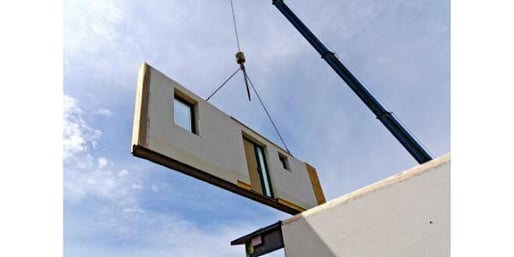
Andru made another great point about reviewing contracts as well before going back to work. Jobs are going to be delayed; it is inevitable. Before COVID-19 many contractors would have 60 workers on a job, and now, only 20 are allowed. This will slow down the process as there are not as many workers on each job site. When reviewing contracts, make sure to understand how much you are responsible for the delay, and how much you can claim to recover some of your loss.
Keeping Employee Motivation
Another question came through asking about employee motivation and how to keep employees busy and motivated. Andru talked about his experiences at Eaglestone and how they have created a remote learning facility for their employees. Now is a great time to widen the gap between you and your competitors. A great way to do that is by getting educated about tools and different mechanical contractor trends that can help you at work. Some of the education they offer are OSHA courses, Excel courses, and eSUB courses. Each of these courses comes with a certification as well. Now is a great time to do these classes and certifications that you didn’t’ have the time to do before.
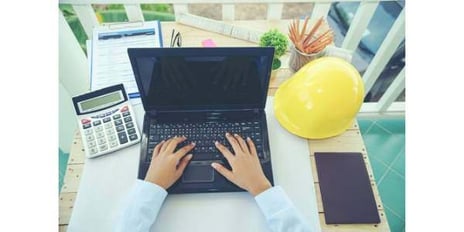
Discussing online courses a bit deeper, Jeff shared how eSUB offers many “how-to’s” available for people. Some of these include how-to-use Slack, how to use SharePoint, how to use Onedrive, and how to use Zoom.
Ryan shared that at UMC, cameras were sent to all their employees so they can get connected with each other. It is critical to continue to get this interaction with one another because many of us only leave the house to get groceries. On the mental health side of things, it’s important to interact with each other to stay motivated and connect.
To wrap up the webinar, all three guys agreed that we are in this for the long haul. That being said, preparation is key. It costs nothing to be prepared but saves so much time and effort later on. It’s important to focus on the positives coming out of this experience and to support each other at this time.