8 Construction Risks Facing the Construction Industry and How to Reduce
Construction is a risky industry. Each project is unique and individualized, with its challenges and outcomes. Risk can appear in any form and at any stage of the construction process. Lack of risk mitigation can result in threats of budget, profitability, efficiency, and project schedules. One of the trickiest parts of the building process is identifying and managing construction risks. With thorough planning and risk mitigation, it’s not impossible.
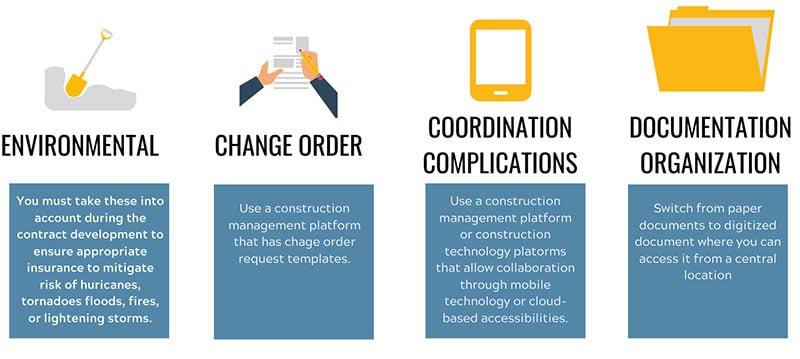
Risk management is critical for every company. Having unknown risks can make a company vulnerable and unprepared for what’s to come. A construction risk management process helps project managers predict where risk can come from and identify projects that are susceptible to cost overruns. With software and project management solutions, risk mitigation is easier than ever before. However, software only does so much; project managers must be familiar with construction risks and how to reduce them.
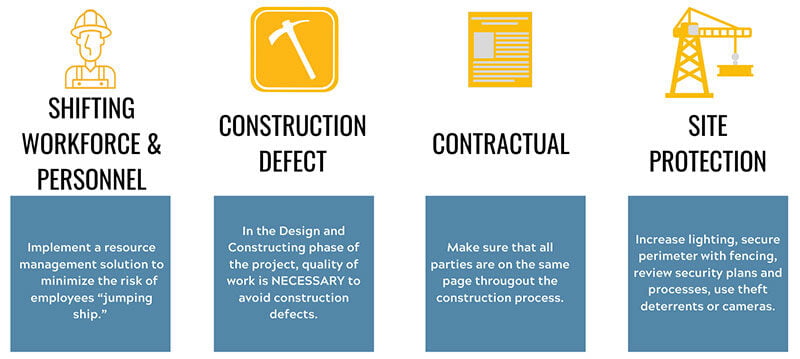
Table of Contents
Construction Risks Fall Under Three Categories:
To fully grasp the idea and importance of risks in the construction industry, it’s crucial to understand the main construction risks first. Construction risks fall under three divisions: Safety, Finance, and Schedule.
Safety
According to USA Today, the construction industry is one of the most dangerous professions in the country. Job sites place safety as a significant priority. Project managers implement daily safety checklist inspections because failure to pass inspections can place a hold on production if there is a need for reinspection. Not only do job site inspection checklists help prevent injuries and fatalities, but they are also mandatory standards, and they list processes and procedures to follow. You can also implement weekly toolbox talks to mitigate safety risks.
Financial
Construction managers assume financial risks because of unplanned costs and material waste. To produce more accurate estimates, try tracking actual labor hours and production units closely. Accuracy also can reduce going over labor hour estimates and overordering materials. Also, there are other risks outside of your control, such as the owner not having enough money to complete the project or late payments.
Schedule
Poor scheduling can drastically impact the construction project’s budget. Any small hiccup in design, constructing, or outside factors can set your schedule back, stretching the duration of the project. Furthermore, an impact on schedule can result in miscommunications with shareholders, clients, and workers.
Shifting Workforce and Personnel
The construction industry faces a skilled labor shortage, an aging workforce, and an inflow of more and more inexperienced workers that are increasing injuries and accidents on job sites. According to the Bureau of Labor Statistics, the projected change of employment from 2018 to 2028, is 10% faster than average. Because of the increased demand for skilled workers, some company’s are moving towards using automated technology. The construction industry uses robotics to complete vertical tasks like excavation, drywall installation, painting, and roofing. The risk of a shifting workforce can be reduced by using automated technology by doing the following:
— Cuts down labor expenses
— Takes less time to accomplish a task by working longer shifts and into the night
— Performs tasks faster
Another way to reduce the risk of the lack of skilled personnel is by implementing a resource management solution to minimize the risk of having employees “jump ship” and leave.
Construction Defect
A construction defect is a deformity in the design, workmanship, or materials used on a project that causes damage to a structure, person, or property. The two common types of defects are design and workmanship. Design defects are typically from the engineer’s or architect’s lack of accuracy on drawings or documents. These are discovered during construction and require redesign or replacement of specific components or even a submittal of a change order. Examples of workmanship defects are improperly installed weatherproofing systems, soils that were not properly compacted, or improper lighting. On the topic of constructing improperly compacted soil conditions, the infamous Leaning Tower of Pisa leans because the builders didn’t check the surrounding soil conditions accordingly.
This risk relates to the quality of labor work. General contractors try to avoid hiring the wrong subcontractors, but it happens. Ultimately, every start of a project comes down to who you choose for the job, do your homework by researching the people you want to be working with on your team.
Contractual Risk
Contractual risks are risks placed on subcontractors because of the agreement between owners and general contractors. A contract could possibly add a penalty to subcontractors or even reduce payments if a job isn’t completed on time. You need to acknowledge risks in construction risk management because these contracts are used to bend remedy provisions under the Workers’ Compensation Act. This provision gives workers compensation in the event of injury whilst protecting the employers from being charged for liability for the injury or workers on the job site. Commonly, the subcontractor doesn’t know that they’ve waived their remedy provisions until the occurrence of an injured employee.
Site Protection
Unattended and unprotected job sites can result in damage to frozen or leaking pipes and theft or vandalism of equipment and materials. Not all sites have extensive security on off-hours, and unattended job sites are susceptible to damage and vandalism. Ultimately, a fenced or well-lit site has a less likely chance of vandalism compared to a site with nothing guarding it. Estimates state that there are approximately $1 billion a year in losses from theft and vandalism. Additionally, that number of losses and costs to builders and companies rose 10% since 1996 and is predicted to continue increasing. Here are some tips from For Construction Pros to secure your job site:
- Increase lighting in off-hours
- Let employees know that the boss is paying attention
- Schedule supplies only as needed
- Keep good records with documentation
- Practice effective inventory management
- Secure perimeter with fencing
- Review security plan and process
- Use theft deterrents or cameras
Environmental
It is important to consider the conditions of the site because natural disasters do happen. If your job site is near a fault line, you, as the Project Manager should consider the risk of earthquakes. It is hard to predict a natural disaster, but it can never hurt to be prepared. Natural disasters include but, not limited to:
Hurricanes
Tornadoes
Floods
Fires
Lightning storms
Managing Change Orders
A change order is a specific type of documentation that you use to record an amendment to your original contract. Change orders consist of the additional work completed that is not specified in the contract. Common causes for change order requests are:
Incorrect estimate of a project
Team or client reached an obstacle that steered away from the original plan
Team or client is incapable of completing their deliverables within budget
Extreme weather or job site conditions cause delays in work
Typically, contractors split change orders into two sections: the price and scope of work. The scope of work is necessary to determine the precise amount of materials, labor, and time needed for the additional updates. The change order process isn’t difficult; however, sometimes people forget them, and that results in falling behind schedule and payment disputes. Read our simple steps to create a change order request so that your client and your team are on the same page.
Coordination Complications
In any industry, miscommunication occurs. But in the construction industry specifically, a mishap or delay in communication can push back a project schedule and risk the overall success. Picture this, you’re a subcontractor that specializes in electrical, and due to the lack of communication, a change order is late; the HVAC sub or plumbing sub might be delayed or have to work around you. Miscommunication can result in simultaneous delays in schedule and the possibility of cost overruns. In terms of risk management, coordination complications are very crucial to think about because it can lead to the waste of unnecessary materials and pricey reworks.
Construction management software is a great way to reduce coordination complications. They allow collaborative engagement through mobile technology and cloud-based accessibility. Implementing software into your management operations can help get subcontractors, contractors, and PMs all on the same page.
Documentation Organization
Document control is one of the construction industry’s biggest risks. Proper document management is one of the PM’s most tedious and time-consuming tasks. Construction projects require hundreds, maybe thousands, of documents that would take laborious effort to sort through and file. Nowadays, contractors are transitioning from paper documentation to digital documentation. Additionally, construction software platforms use cloud-based technologies that allow you to search for any document at any moment, reducing schedule delays and the accessibility in a central document location.