6 Construction Strategies to Reduce Inefficiencies & Improve Profits
The concept of construction project management has changed drastically over the past decades. It is now more important than ever for companies to have experienced project managers to helm activities on their construction sites. They are responsible for forming a complete management strategy to not only manage the construction process, but also to reduce inefficiencies and improve profits. Here’s how to do that.
Table of Contents
6 Construction Strategies to Improve Profits
Gaining a competitive advantage in construction starts with skillful management. From setting performance metrics to aligning resources, the right on-site management strategy determines whether the project gets delivered on time. While difficult to implement for some companies, here are some of the best construction strategies to consider if you are looking to strengthen a project’s management.
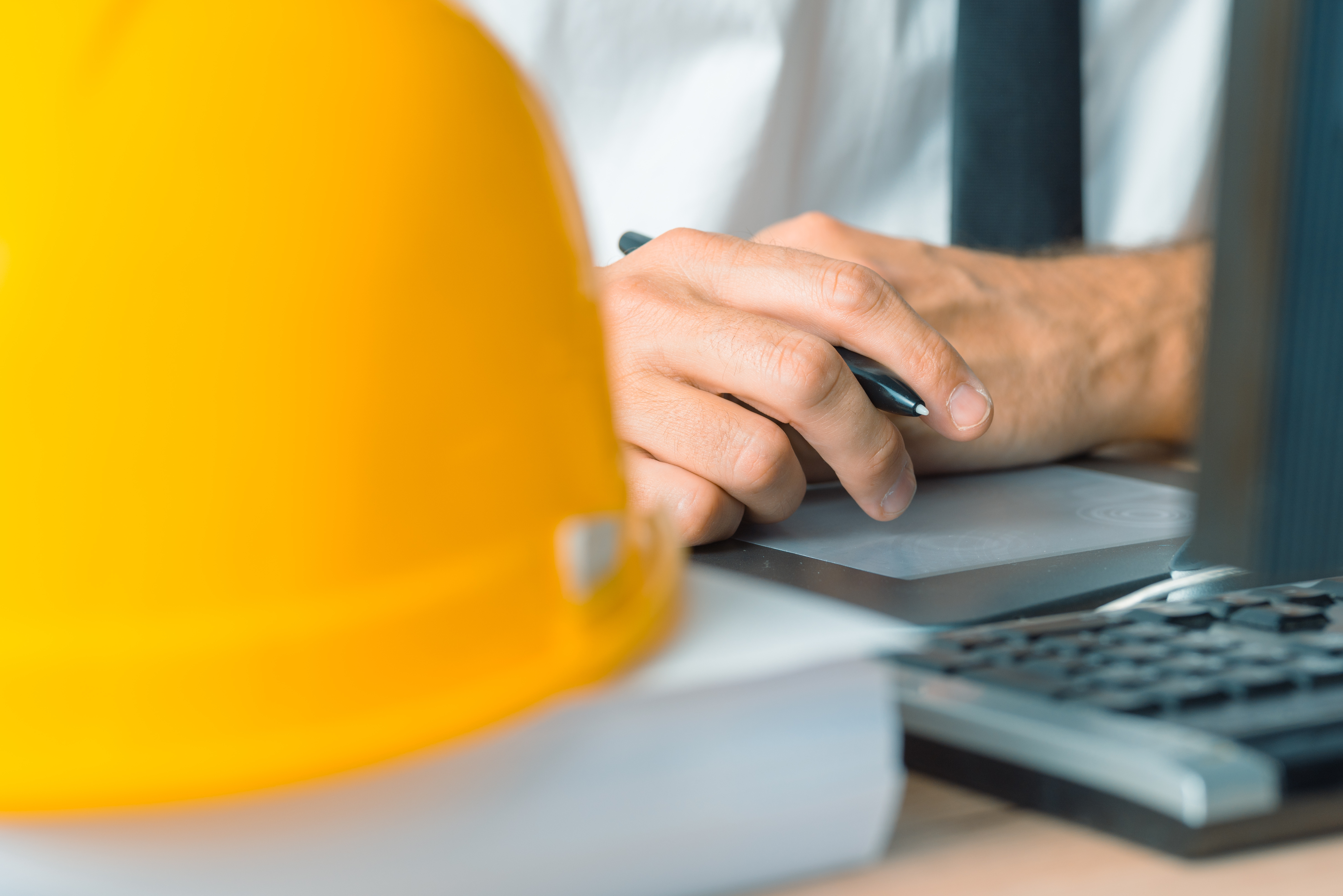
1. Implement a Project Management Software
Managing a construction project can be challenging without opting for digital solutions. Automating construction operations leads to a more collaborative and continuous workflow regarding communication and data. Employees also reduce inefficiencies by tracking their work and optimizing daily tasks.
For example, using project management software to archive documents reduces the time to sort through piles of paperwork. The best construction platforms in the market can also provide cloud-based tools to monitor real-time updates from both on- and off-site workers.
Hence, project management software becomes one of the most critical construction strategies for successful project management.
2. Articulate a Clear Set of Values and Targets
During the early phase of construction, project managers should sit down with their planning team, engineers, architects, etc, to agree on deadlines, objectives, and other targets related to the project. All parties involved must be on the same page to avoid last-minute issues over completion and quality assurance. Creating progress reports will help team members know what they have achieved so far and what to shoot for, nonetheless reducing inefficiencies on the job site.
The following are some examples of efficient operation goals:
Breaking down communication barriers: Daily reports help improve the time it takes to document, communicate, and resolve issues.
Promoting safe behaviors: Setting goals around safety behaviors encourages healthy workers who are ready to move projects forward. They can be a specific percentage of PPE compliance or workers making modifications to correct safety problems within a set number of days.
Improving labor productivity: Tracking time towards job costing allows construction companies to use historical information on actual costs against estimates to offer more accuracy in estimating.
Ensuring client satisfaction: Comments provided by customers will determine steps you need to take to improve those scores. Thus, shedding insight for improved delivery of future projects.
While it may sound simple, estimating benchmarks can be incredibly difficult. However, they are necessary to develop accurate project plans. Discuss your business trends, the yearly overhead cost, and desired profit so you can set your business goals and the actionable steps to achieve them.
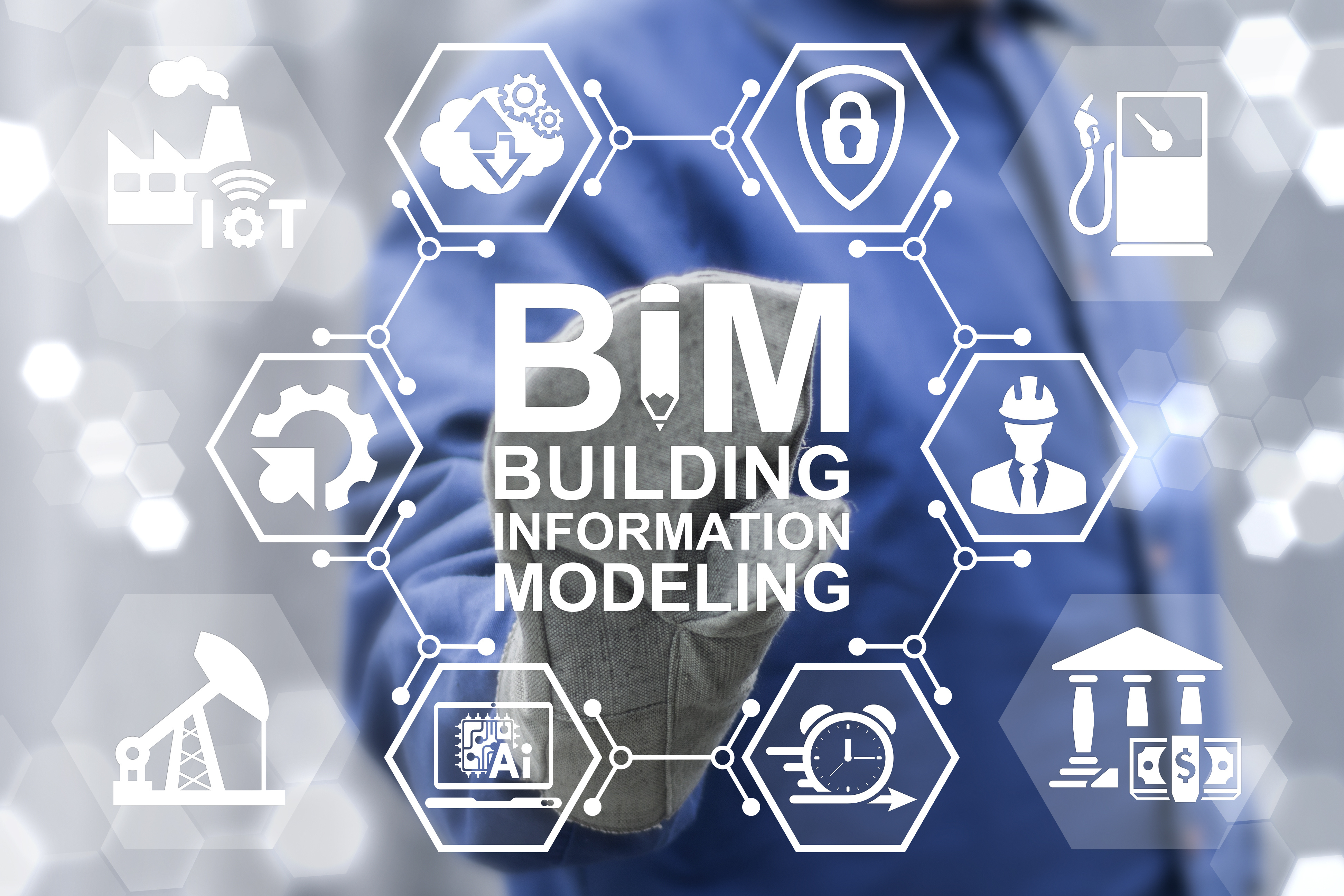
3. Base Construction Plans from Data
Every project must have a solid and clear plan in place before the start of construction. The more developed and prepared the plan, the higher the productivity rate of the project. Hence, utilizing an improved data-driven construction strategy becomes necessary to stay organized and reduce inefficiencies, especially for large-scale projects.
One example of a data-driven plan is BIM (Building Information Modeling), a popular strategy to improve project delivery. It extracts data and enables all project workers to see their performance data and schedule maintenance as needed. Its main advantage is to highlight on-site issues before they become too big (or too expensive) to handle.
BIM is a useful tool to use in the planning process because it can predict job costs by calculating the cost of building materials and estimating the duration of a construction project. Ultimately, when employees understand the workflow from the planning phase, it prevents mismanagement and resource misallocation, and, most importantly, reduces inefficiencies.
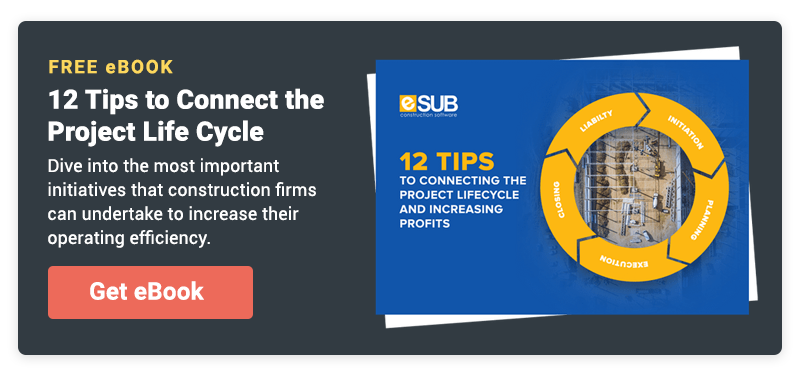
4. Include Training Programs in Operations
Finding experienced workers can sometimes be challenging. Providing substantial training for construction teams ensures everyone is knowledgable and prepared to complete tasks safely and efficiently. That being said, project managers may write off training programs because they are either expensive or unnecessary at the start of construction. While true in some cases, training workers is always a long-term investment that ultimately yields profits.
Here are a few examples of construction training programs:
Project planning: Assures you train your engineers and managers in processes designed to produce predictable workflows.
Contracting strategy: Consider proven methods like activity-based cost accounting, such as daily reporting) that help reduce costs and improve productivity.
Performance management: Establish performance targets for workers to meet and measure how to do so within their budget.
Change order management: For instance, teach workers how to create a detailed change order.
Project risk management: Instruct risk-assessment methods and ensure the knowledge of possible outcomes and solutions.
Contract management: Explain to the team the terms and conditions of the construction project. Includes construction strategies that your company intends to implement.
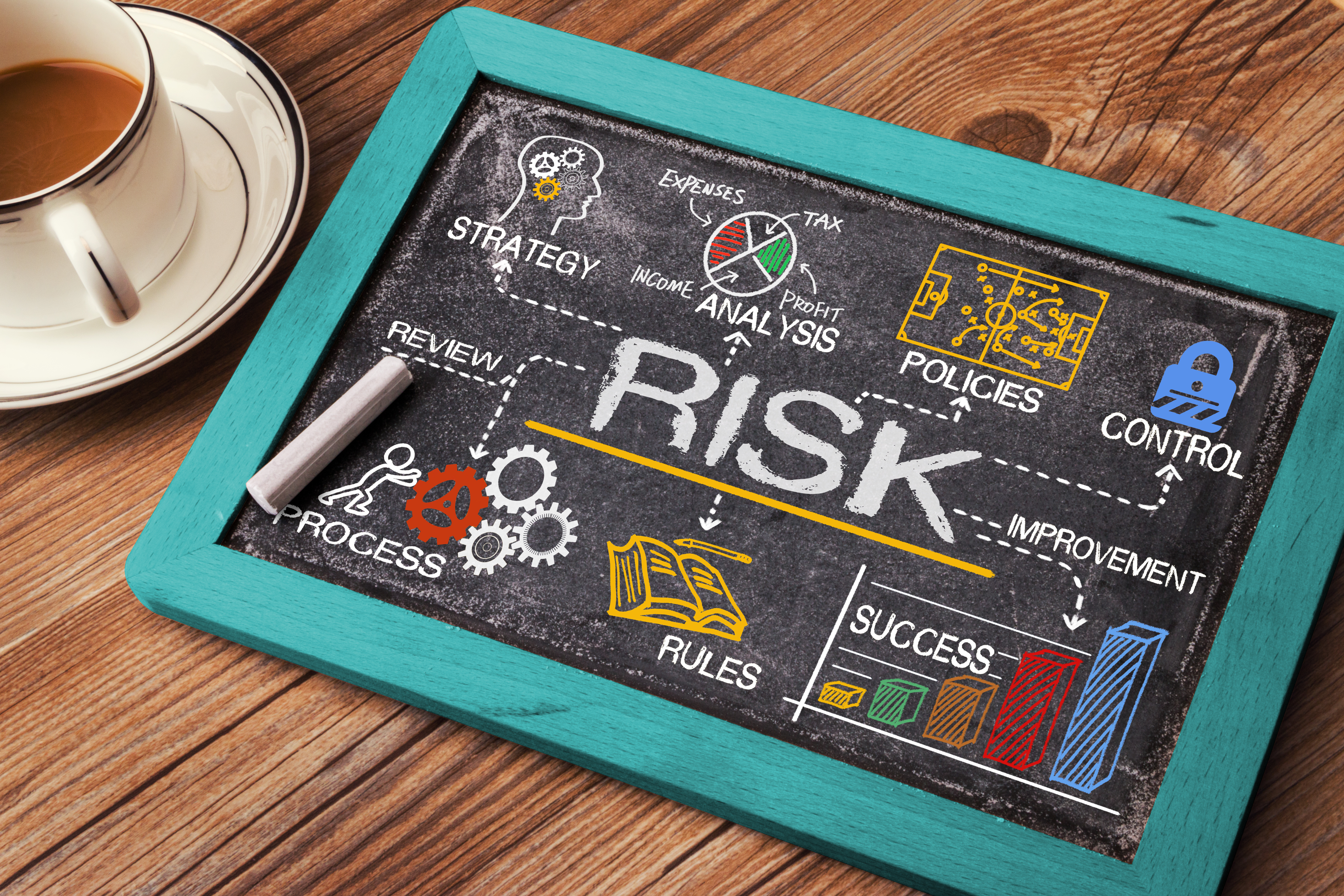
5. Determine the Right KPIs
Key Performance Indicators (KPIs) measure whether a project has been successful. Many contractors concentrate on tangible indicators like financials because they are easy to measure. However, several other measurement metrics are essential to improve efficiency in construction operations.
Here are some KPI examples project managers may want to monitor for their projects:
Safety: The incident/safety rate, number of safety meetings/communications, and number of accidents per supplier.
Quality control: The number of defects, time taken to fix errors, customer satisfaction, cost of reworks, number of site inspections, number of passed site inspections.
Employees: The turnover rate, employee reviews, and training completion rate.
Performance: The percentage of wasted time (equipment & labor), mean revenue per day/hour, and amount of waste.
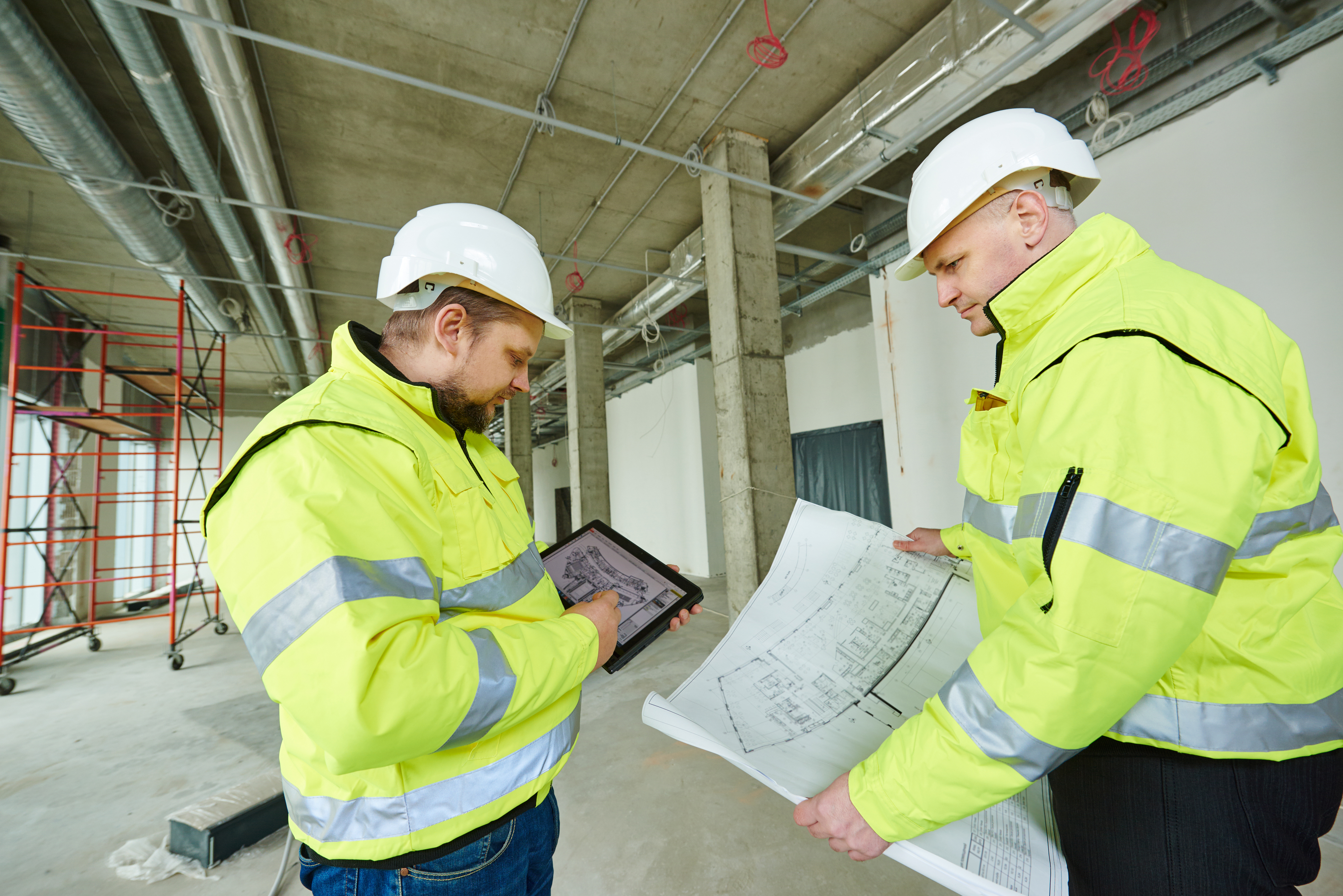
6. Regulate Profitability and Track Costs
Finally, regulating profitability and tracking costs is another leading construction strategy. As a Project Manager, you want to reach your profit goal. To do so, you must keep your costs down and complete the project within the scheduled completion date. If you want to operate more efficiently, tracking construction costs by using job costing is an excellent way to determine labor productivity. Project managers should be on top of materials management and organize the job site to let their workers be as productive as possible.
Therefore, tracking costs on change orders can increase your profit margin because it makes billing easier for construction accounting. Proactive project management contains tracking time cards towards job costing to catch early indicators that the project is going off-budget.
Conclusion:
Adapting new operating models in the growing construction industry can be challenging for your management. For most companies, implementing any of the construction strategies listed above will require a significant reform in their company culture. However, the reform will be worth the time and effort in the long term by helping reduce inefficiencies and improve profits. Companies that understand the need for change put themselves in a winning position because they achieve results in higher productivity and profit.
Make eSUB Your Strategic Partner for Construction Project Management
Adopting a cloud-based project management software like eSUB forms a cornerstone for an excellent construction strategy. It is specifically designed for subcontractors, and can also be tailored to each project. The digital platform makes document management more efficient by providing project visibility and necessary real-time updates to spot and fix small issues before they become too big.
With a centralized database, eSUB ensures all workers and stakeholders have access to all documentation, helping mitigate risks and preventing claims. Furthermore, an easy-to-use interface streamlines work to let project managers, contractors, and executives quickly optimize on-site tasks.
If you are interested in a top-rated project management software to improve safety, lower insurance costs, and more, schedule a demo to learn how eSUB can help.