The Benefits of Prefabrication in Construction
Table of Contents
What is Prefabrication?
Prefabrication is the process of making buildings, or components of buildings, in a different location than the job site itself. Construction companies will transport the completed unit to the final site, where they will also complete the setup and handover buildings to their new owners. This process eliminates the need for traditionally sourced construction materials because off-site assembled parts result in less waste. As the raw materials are built off-site and shipped partially assembled, prefabrication reduces the cost of labor and the cost of materials.
There is controversy regarding prefabrication because, in the past, it was a low-mass development method. Prefabrication is getting more and more relevant in the construction industry, but more significant in commercial construction. However, civil engineers use prefabrication the most because mass amounts of pre-assembled concrete and steel sections are made then transported to sites.
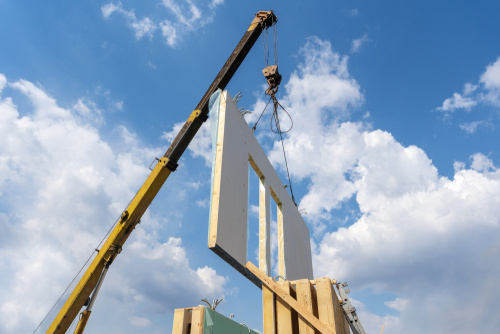
Benefits of Prefabrication:
1. Impacts Technology Trends with Advanced Design Tools
The construction industry has reinvented prefabrication and modularization due to the innovations in construction technology. BIM (Building Information Modeling) technology is a useful tool that is making the construction industry more environmentally sustainable and economical. BIM combines technology and construction to help contractors and companies visualize the scope of the project. The integration of technology and construction can visualize the cost and material differences, which can, therefore, reduce construction material costs and wasted labor hours.
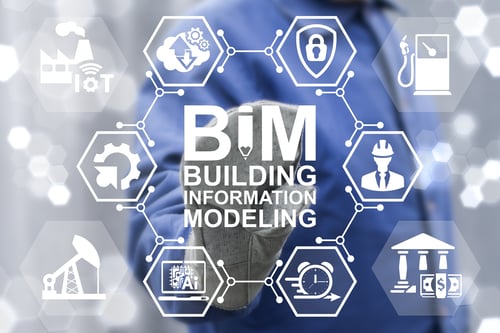
2. Better Safety & Security
Construction is a hazardous industry to work in, so companies want to implement safer processes. With prefabrication, there is less risk for problems with dirt, moisture, and other environmental hazards because workers create sub-assemblies in factory-controlled environments. Recently, prefabricated materials and engineering have improved to make the structures and assemblies as strong as traditional buildings. On job-sites, the workers and possible tenants susceptible to weather-related health risks, so a factory-controlled climate ensures more safety compared to a project job-site. Additionally, there are more strict factory procedures and processes that protect workers from on-the-job injuries. Although construction sites prioritize safety, workers have higher chances of injury because of changing ground conditions, weather-related conditions, and wind.
3. Cost-effectiveness
The construction industry faces an increase in construction costs annually, which makes profit margins smaller each year. With temperate weather and longer daylight hours creates an increase in demand for materials and labor, which drives the price up for both. Prefabrication reduces the cost of labor, further offsetting the rising costs of materials.
There is a hotel expected to open in the late 2020s that will be the tallest prefabricated structure. Marriot’s AC NoMad Hotel in Manhattan, New York, is in the process of being assembled and is set to stand 26 stories high. Because this project is using prefabricated methods, Marriott can minimize labor costs and waste because the building will only take 90 to assemble. In terms of costs, it would cost approximately $70 M to construct this building, but in New York City, the cost of a comparable building would cost $100 M.
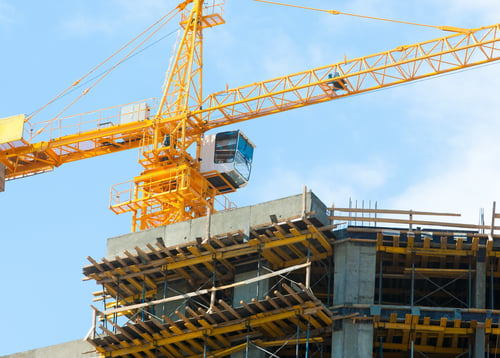
4. Consistency & Quality Control
Factory tools used in prefabrication offer additional quality assurance compared to repeated construction on-site. Sub-assemblies in prefabricated construction are produced in a controlled manufacturing environment and follow specified standards, therefore built to a uniform quality. On construction sites, the workers in the process have skills that vary at different levels. Still, with prefabrication, an experienced worker builds a component in weather-controlled settings that have standard quality checks throughout the build.
5. Flexibility
Without difficulty, workers disassemble and relocate sub-assemblies to different sites. General contractors and owners are leaning more towards prefabricated methods of construction because it provides flexibility without constraining creativity. Opportunities are endless because prefabricated and modular construction allows for the flexibility in the structure design.
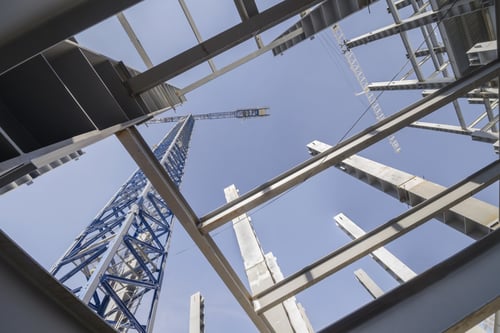
6. Green Construction
Compared to traditional construction, prefabricated and modular buildings are more eco-friendly in both the short-term and long-term. Traditional construction processes require more materials that lead to more waste. Prefabrication has a lower environmental impact because extra materials are recyclable. Whereas, on a traditional site, waste goes directly to a landfill. A factory’s controlled environment allows for better air filtration for better wall insulation, which directly increases efficiency for energy.
7. Saving Time and Accelerating Construction Process
With prefabrication, it takes a significantly less amount of time to build compared to on-site construction. In fact, it takes less than half the time compared to traditional on-site construction. Prefabrication takes less construction time because of the precise planning, elimination of on-site weather conditions, and simultaneous construction of multiple assemblies. Shorter construction times allow construction companies to take on numerous projects at once, allowing businesses to grow instead of focusing on one project at a time.
Final Thoughts
Prefabrication is a modern construction process that is growing in popularity. In the construction industry, there are innovative ideas and approaches that increase productivity and cost savings. All in all, prefabrication enables time and cost savings, quality control, and a more eco-friendly construction process.