5 Different Types of Pipe Inspection
Inspecting pipes and plumbing connections is essential for many home and property owners. It is a standard procedure step for a larger process in building and selling homes. It is also a necessary step in renovating old properties to find and plug leaks, replace old pipes, and such.
Something important to note is that different buildings have different structures and pipe locations. You cannot take a one-size-fits-all approach to assessing and inspecting them. Here is a close look at the different types of pipe inspection various contractors use to examine pipe systems.
Table of Contents
The Types of Pipe Inspection You Need to Know
Every pipe inspection method requires tools, machinery, and the skill and knowledge to put them to use. It is important to choose the inspection method based on how quickly and efficiently a job can be completed. Pinging pipes when a wall will produce expensive results. The same can be done less expensively. So, make sure to put your clients first.
Visual Inspection:
The process is just what the name implies: the plumber takes a visual look at the piping to see if any problems could become outstanding issues, such as small blockages, deteriorating pipe sections, etc.
This, however, requires the piping to be completely exposed and accessible, such as in a basement or under a sink. Hence, if possible, a visual inspection is always the first choice for a plumber because it gets the job done faster.
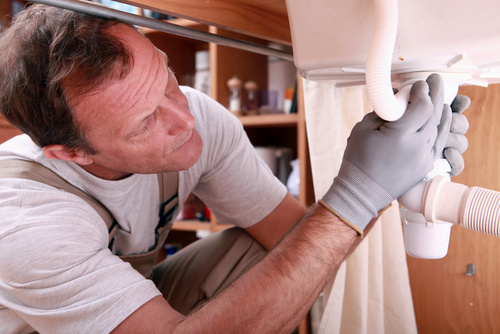
Push Cameras:
Where visual inspection is not possible, the next easiest option for a pipe inspection is using a push camera, commonly referred to as a “pushcam”. It is essentially a camera attached to the end of a long cord. The camera is pushed through a pipe, and a live video feed is streamed through the cord to the plumber.
This allows a plumber to get a visual look inside a pipe, which would not be possible otherwise. However, there are some limitations when performing complicated movements with the cord. A push camera, for example, cannot inspect branching lines in a pipe section.
Lateral Launch Cameras:
When inspecting complex or deep piping systems, a plumber must rely on lateral launch cameras instead of push cameras. The mounted camera system is inserted into the main line just as with a pushcam. When the camera reaches a branching line, though, the mount can be adjusted to change directions before launching a second camera into the new area. The plumber can then inspect the piping via the live video feed.
Robotic Crawlers:
The advent of solo robotic crawlers is the next stage of pipe inspection in modern-day construction. Unlike other cameras, the plumber does not physically control a cord during inspection. The robotic crawler is programmed with specific parameters based on the pipeline and then launched inside. It will then continue to explore and inspect the designated areas on its own, changing directions as needed without any manual input while sending live video footage for the plumber. When the inspection is over, the robotic crawler finds its way back to the start of the pipe for retrieval.
Sonic Location Tests:
While not applicable in most situations, sonic location tests come in handy when the only option left is to break down an entire wall to find the source of a leak. By using specialized machinery to hear the sound of leaking water on an ultrasonic level, a plumber can narrow down the source of a leak from behind thick walls. This reduces the amount of demolition needed and makes the job more efficient.
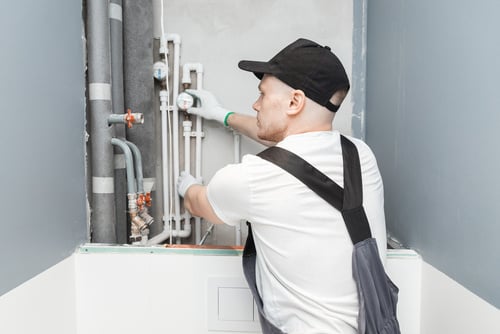
Common Issues Related to Pipe Inspections
Many property owners who call for a pipe inspection do not necessarily have an acute issue that needs fixing. Many are having a pipe inspection done as a preventative measure for the future.
In this case, it falls on you as a plumbing contractor to know the potential signs of trouble and communicate them. Even if it does not affect their plumbing now, it may later, and the better you communicate this, the more trustworthy you will be.
Roots and Blockages
Roots are some of the biggest problems faced by plumbers when inspecting the main sewer lines. While residents with large trees nearby will likely be a bit more proactive here, a pipe can be infested with roots even if there are no trees around. This is due to the combination of moisture and nutrients in drain lines.
Sometimes, though, there are blockages from non-plant matter, like something being disposed of incorrectly.
General Deterioration
Here is an interesting fact. Cast Iron has a lifespan of around 50 to 60 years. Hence, an older home that never had its pipes replaced may be in dire need of inspection. Old pipes mean more risk for cracks and leaks. It is always better to replace them before they burst.
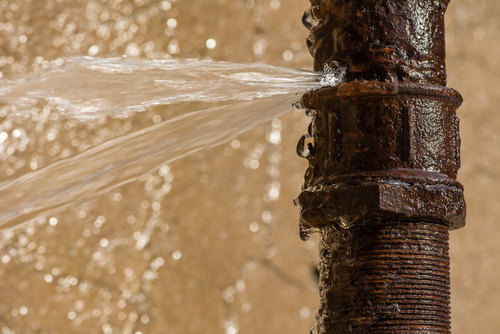
Incident-Related Damage
Sometimes, after an accident or natural disaster, people may want a pipe inspection to determine the scale of damage to their plumbing, if any.
Ultimately, the more types of pipe inspection tests that you can provide, the more clients you can service. As a result, any plumbing contractor business should work to make sure they have all the tools necessary to properly service their clients.
How eSUB Can Help
eSUB is a cloud-based project management platform built especially for subcontractors. It seamlessly integrates with leading construction software systems so you can easily switch from your current document process to a cloud-based system to upgrade your construction project management process.
eSUB organizes all your project information in one place, allows for smooth collaboration, and streamlines communication through its intuitive interface. It also works on your mobile to let you track projects on the go—no matter where or when—and stay up-to-date.