Understanding When To Build With Steel vs. Concrete
We are reliant on certain materials as the fundamentals of structures across the world, and both steel and concrete fit neatly into these categories. Each of these has the durability, versatility, and accessibility to make them commonplace in practically any construction project. However, one issue that a lot of construction newcomers might be dealing with is whether or not one is better than the other. Is steel stronger than concrete? The easiest way to do this is to look at some of the most important traits of building materials and determining how steel and concrete measure up.
Table of Contents
Strength
So, with that in mind, is steel stronger than concrete? Naturally, durability is going to be one of the first questions that come up with any construction material. Ultimately, steel wins out, but concrete is far from poor in this regard. Concrete structures are easily resistant to fire damage, wind damage, and pests. This makes them easily more appealing than, say, wood or stone. However, because it’s cast-in-place, concrete is vulnerable to earthquakes, as it can crumble or crack.
By comparison, steel is also resistant to pests and the elements, though it may have some trouble with extreme heat. It’s the earthquake factor that leads many people to give steel the slight edge, though. By nature, steel is ductile, which makes it easier for the frame to absorb energy. Steel members also have the ability to rotate slightly at the joint, making it harder for it to separate in the event of an earthquake. With this said, not all regions of the world have a severe earthquake risk, which may make concrete preferable for other reasons we will cover.
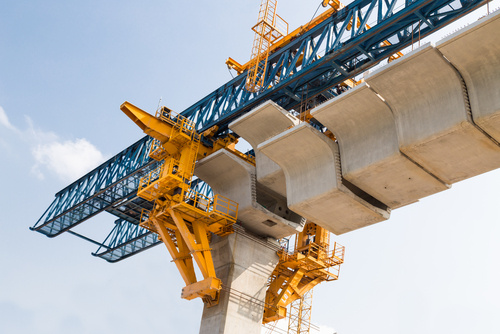
Versatility
Another early question that needs to be discussed is what material is the best to create your chosen design with. There are pros and cons to both concrete and steel here. For one thing, the initial semi-liquid form of concrete is a major plus in its favor. You can create just about any concrete form if you have an appropriate mold. However, concrete is also extremely heavy, meaning that if you want to, say, make a large span, you would need support columns. In the case of steel, your easiest prefab shape would be a typical rectangle. While there are other possibilities, it may represent a higher cost. However, steel has the ability to span a long distance without needing interior columns. So, for example, for an air hanger, this framing option would be ideal.
Size is also something to consider. Reinforced concrete is excellent for massive projects like dams or bridges, but wide spans may be impossible to cover. Pre-engineered steel buildings have no limitations in terms of length, which makes them ideal for wider setups or buildings that require a soaring ceiling.
Availability
In this case, supply isn’t necessarily a huge concern for either material. With that said, concrete does win out, simply because the base ingredients to create concrete will almost always be available and cheap. These are:
- -Sand
- -Gravel
- -Water
- -Cement
The only exception is in the case of natural disasters, where there is a huge demand spike at the same time. When it comes to steel, between U.S. steel capacity and fabrication shops, there is generally always enough material as well. However, getting the steel you need might be a financial issue, as we will cover in a second.
Cost
Naturally, the bottom line is going to be a top priority when it comes to choosing a construction material. And while other material costs have spiked, ready-mix concrete prices are relatively stable. In terms of actual construction costs, opting for a cast-in-place style can be more expensive upfront but generally gives strong ROI across the board. How so? For one thing, insurance companies will have a lower liability due to the increased safety of this method.
With steel, the cost proposition is a bit of an interesting one. The higher durability of steel means it’s possible to create a stronger building with less material. However, steel prices may be higher than in the past due to tariffs being implemented. Companies can try to reduce their costs in this area by using recycled steel or taking advantage of production innovations to have their steel created faster.
We should also discuss the costs of building as well as the costs after building with the different materials. Concrete is generally the more expensive option here, in terms of financial and time costs. To implement it, you need skilled professionals and to wait for the concrete to cure. Steel can be implemented faster due to prefabrication, allowing the actual construction to be a lot faster and require fewer skilled workers.
But what about the future? Steel generally wins out. Being more durable means fewer upkeep costs overall. However, one benefit that concrete does have is being able to save money on cooling and heating. The mass of concrete cuts down on shifts in temperature.
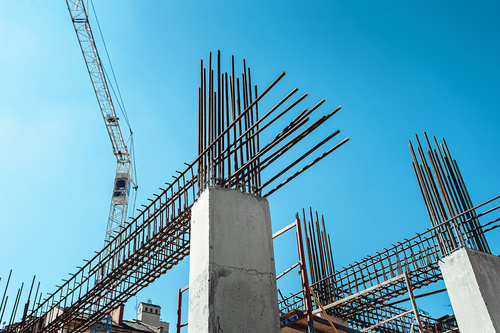
Is Steel Stronger Than Concrete?
So to answer the question, ‘is steel stronger than concrete’, it depends on the use. In many cases, factors like durability or aesthetics mean that steel or concrete is an obvious choice for your next construction project. However, let’s say that both are technically suitable for the job. This means that the issue largely hinges on preferences, but also cost. For one reason or another, it may be less expensive to opt for steel over concrete, or vice versa. You also need to consider costs outside of the raw materials, like how long it takes to install the different items as well or how expensive upkeep is.
Construction companies need to take a data-based approach in order to excel in this area, which means needing project management software such as eSub to do the job. How exactly does this work? By tracking your employees and materials, you get a full understanding of how much it may cost for you to use steel or concrete in a given situation. Combine this with a historical record of your past jobs and you’ll understand exactly what the best fit is for a future job.