The Basics of Sheet Metal Fabrication
Metal fabrication is often a foreign area of construction or engineering to those who aren’t fully immersed in it. The fabrication process refers to shaping, bending, and generally manipulating the sheet metal to different shapes and sizes. Typically, production involves the transformation of sheet metal (of varying levels of thickness) into equipment. For this reason, it is usually more accurate to describe sheet metal fabrication as a collection of forming techniques that, when combined, produce a part or construction feature.
Because sheet metal fabrication is such a niche industry, it can prove invaluable to hire a metal fabricator who is familiar with all of its nuances. A metal fabricator is an ideal match for industrial projects that require the creation of complex sheet metal designs and products. Such features require a detail-oriented approach to what is a tedious, multi-step process from start to finish. These jobs require several skilled experts to combine the fabricated sheet metal with other project features.
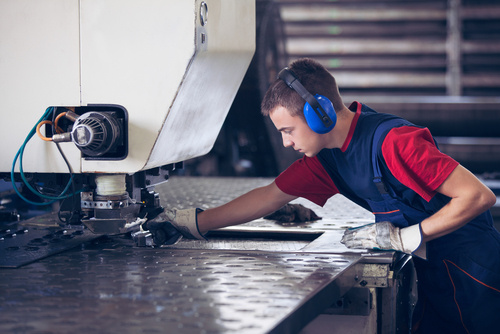
Below is a beginner’s guide to understanding sheet metal fabrication basics from a commercial and construction lens. This distinction is important, considering the majority of sheet metal fabrication occurs in auto-shops, garages, and welding companies.
Table of Contents
Guide to Understanding Sheet Metal Fabrication
Planning
Like most contractor jobs, the project first starts with the drawings and blueprints. As the specialty contractor or project manager, this is also where you would recognize the need for a sheet metal fabrication expert. The blueprints developed by the engineers will determine the sheet metal specifications necessary to create the initial drawings that will be sent to the metal shop or metal supplier.
Since most sheet metal fabrication requires large, heavy machinery, much of the work has to be done off-site before it is brought over for construction. This is why the drawings have to be finalized quickly enough to be ready for installation but be reviewed thoroughly enough to not require adjustments once the metal has been fabricated and brought to the worksite. Once end-product requirements have been determined, the final shop drawings will be drawn and sent out to the metal fabricator for preparation.
Fabrication
There are many different techniques used by professional metal fabricators to form and manipulate sheet metal. Similarly, there are several different types of metals that can be used in the metal fabrication process; these include steel, stainless steel, aluminum, and other soft metals such as copper or brass. Below are some of the more common methods used in sheet metal fabrication.
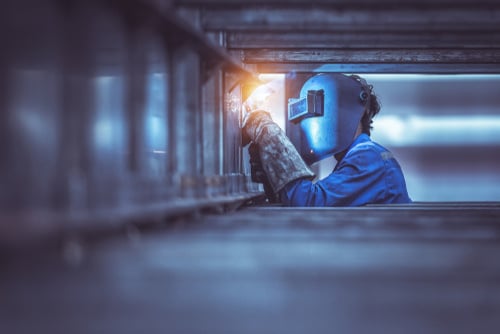
Common Methods of Sheet Metal Fabrication
Cutting
Sometimes sheet metal will arrive at the shop with rough welding edges from previous projects. This can occur because the pieces were leftovers from older jobs, or metal was sourced from recycled materials. Regardless, cutting is often the first step in sheet metal fabrication. Cutting removes the welding bumps while also forming the sharp, clean edges necessary for further manipulation like bending or punching, for example. In most cases, the fabricator will take a rectangular metal sheet and cut it down to the dimensions specified in the final drawings. Larger metal fabricators will use giant, automated machines for absolute precision.
But, like these machines, their surfaces may be expensive or inaccessible. Local fabricators will likely use a stomp shear, instead of a plasma cutter, for laser-straight lines. Cutting with a shear means using sheer force. These machines often are foot-operated and require no electrical element. That said, the size of the final metal product, and the size of the project, may influence whether you seek the request of larger, more industrial firms. Metal fabricators like this will often utilize laser, plasma, or water cutting instead of shearing to achieve 0.1-millimeter precision.
Bending
Like cutting, bending is a critical part of the sheet metal fabrication process. Almost every metal fabrication project requires bending of some kind to form the material to a specified shape or angle. Rarely do construction assignments require just a flat piece of sheet metal. If they do, it is likely in combination with other bent or fabricated pieces. This step, like the name suggests, involves the bending of the sheet metal. Bending in sheet metal fabrication, however, is more akin to folding than actual bending.
While U-shaped bends are popular, so are V-bends and other angled positions. For this reason, accurate bending techniques are incredibly difficult and require a highly skilled manufacturer. This level of difficulty is made worse by the effect of “spring back,” which plagues sheet metal fabrication. To overcome this effect, the manufacturer must expertly overbend the material so that it recoils and springs back into the desired position.
Punching
This is a very common technique used by metal fabricators to punch holes through the sheet metal. Punching is a process that relies on sheer force to perforate perfectly sized holes into the metal. Sometimes punching can be used to create specialized indentations in the metal as opposed to cutting straight through.
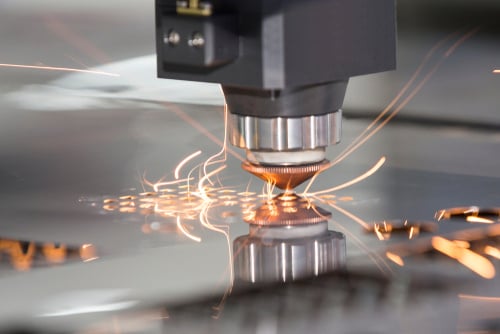
Joining
After the sheet metal has been manipulated and formed into the desired shape, any loose, in-contact sides must be joined together. There are various ways one can join the corners or sides of a sheet metal fabrication. The most common method is welding, but different project specifications can require other processes such as brazing, riveting, and adhesives. Welding requires highly trained professionals to mitigate the safety risks while also producing a small but accurate join line.
Finishing
After the metal has been cut and formed to the project’s requirements, a surface finish must be applied to the end product. This transforms the sheet metal fabrication from its rough, metal aesthetic into the slick, precise final product. Often finishing can include paint and powder coatings, silk screening, or the addition of sealants and other protective layers. Additional finishing treatments can be applied to increase certain existing properties the sheet metal already possesses, such as increased resistance or conductivity.
Final Thoughts on Sheet Metal Fabrication
Sheet metal fabrication is an art and a science. With its wide range of techniques and nuance, there’s no doubt that you will need a skilled metal fabricator should your project ever require formed sheet metal. eSub makes managing these types of specialty contractors even easier by creating a cloud-based, document-sharing network. Receive RFIs in an instant, and keep your metal fabricator up-to-date with the latest drawing revisions. Make your job easier with eSub.