How to Deal With (and Prevent) Commercial Building Delays
As nearly anyone who works in commercial construction will tell you, delays are a big problem in the industry. How big? A McKinsey study found that a staggering 98 percent of megaprojects (those with budgets over $1 billion) faced cost overruns or delays. Another study found that 60 percent of construction cost overruns at all budgetary levels are due to a combination of commercial building delays, diminished productivity, and weather. You can’t do anything about the weather so it’s time to figure out how to work on the rest.
The amount of coordination required to execute any large construction project makes commercial building delays virtually inevitable. But it’s how you plan for, mitigate, and deal with those delays that can make or break your project. Here are four key tips for avoiding delays on your construction project—and minimizing their damage when they do happen.
Table of Contents
1. Ensure that your schedule is realistic and prioritize elements you know could take time
No contractor wants to tell a client that a project will take longer. And no client wants to hear it, either. But what’s far, far worse is getting the news after the fact, when deadlines are about to start flying past.
A good, realistic schedule leaves room for dealing with issues as they arise. That process begins with identifying likely trouble spots for your project and leaving space in your schedule to address them. Several common sources of construction delays include:
— Permits: Local zoning and permitting processes are often a major source of commercial building delays, especially in large cities. Well-run commercial contractors should have someone with knowledge of local permitting on staff or on retainer.
— Long Lead Materials: Some materials simply take longer than others to fabricate and/or deliver. HVAC systems are a particular pain point since they’re usually custom-fabricated for large projects.
— Shop Drawings: This is a process you definitely shouldn’t wait on, as shop drawings have many critical downstream effects. The longer you wait for these, the longer you will typically wait for your materials.
— Bonding: Getting the terms of construction contract bonds worked out can be a challenge, so it can be a big advantage to use a licensed commercial bonds dealer that works directly with carriers. You’ll likely save time and money on getting bonded.
2. Be aware of environmental conditions.
Creating and maintaining productive working conditions is key to lean construction. An important part of that is maintaining awareness of relevant factors on the ground:
— Public Utilities: Questions of how to work around public utilities should be addressed from day one when planning a construction project. Whether it’s gas lines, power lines, sewers, or public transit, it’s absolutely essential for contractors to coordinate with municipal and state governments to plan around these critical services. The worst-case scenarios can be incredibly bad—just ask the contractor who knocked out an entire island’s power during peak vacation season.
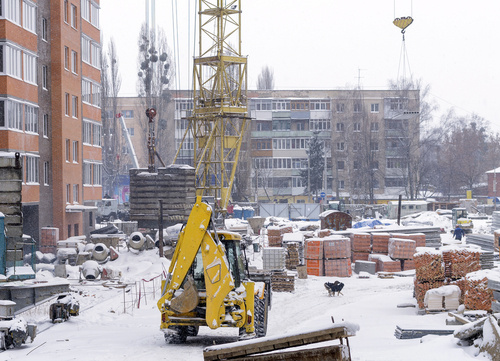
— Weather: The weather, of course, will do what it wants. However, your job site should always be prepared. There are a variety of precautions you can take to protect against inclement weather, and someone on your team should be responsible for checking weather reports to see which conditions might lie ahead. In some states, you may also need to be aware of thaw and frost laws that can affect equipment delivery and deployment schedules.
— Environmental Regulations: Air, water and soil quality regulations exist to keep everyone safe. However, if you’re not planning around them, they can come back to create problems for you when least expected. Learning about relevant environmental rules is especially critical when you’re working near sensitive sites such as streams or with highly toxic materials. Every state and municipality has different laws, so thorough and diligent research is essential.
3. Address change orders as quickly and completely as possible.
No matter who initiates them, change orders are almost always a source of consternation on job sites. However, there are ways to make them less stressful and ensure that they’re completed successfully. Try this six-step method for dealing with change orders:
- Understand exactly how the change order relates to the original contract.
- Review plans in detail to make sure your team grasps the precise nature of the necessary changes.
- No matter what, never ignore or purposefully delay a change order.
- Maintain open communication with all stakeholders, from the executive suite to the job site.
- Negotiate the change order to establish a plan of action and don’t be afraid to push back the timeline.
- Keep detailed documentation of all negotiations, requests, and changes.
A swift and thorough response to change orders can be the difference between success and failure on a construction project. These steps facilitate accountability and transparency at every stage of the process.
4. When commercial building delays happen, prioritize communication to avoid compounding them.
Construction delays tend to have cascading effects that can cause significant issues far downstream of the original problem. In such a situation, it can be easy for a small delay (often due to something as simple as inclement weather) to create a pile-up of problems.
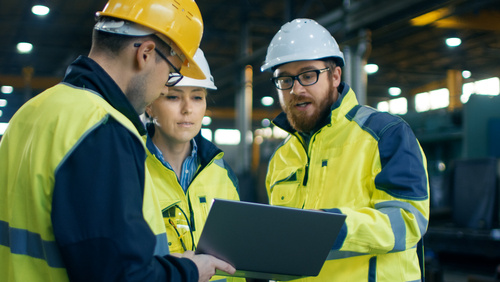
One secret to avoiding these destructive ripple effects is to ensure that communication lines stay open between all parties affected by the delay. This can take a little bit of outside-the-box thinking because there may be more stakeholders involved than are immediately apparent. The list of people you should inform includes, but is by no means limited to:
— Project Managers: Project managers are responsible for coordinating all parts of a project, and so should be among the very first people you loop in on any project delays.
— Subcontractors: Contractors of all kinds often have very tight scheduling, so it’s both a courtesy and a necessity to inform them if projects will be delayed.
— Suppliers: Logistics is a delicate art and can easily be derailed by delays if they’re not communicated well ahead of time. The last thing you want is to have an expensive custom part stuck on a truck because the job site isn’t ready for it.
— Governments: Construction delays may affect public utility schedules and other elements of the government apparatus and, potentially, contract terms and other legal liabilities.
— Financial Stakeholders: They may not be the boots on the ground, but owners and financiers hate to be left out of the loop. Keeping on-the-ground problems away from upper management is almost guaranteed to backfire.
Construction delays can be infuriating and costly. However, in many cases, it’s possible to reduce both costs and frustration through planning, communication, and a little bit of patience. Be aware, be realistic, and, most of all, be honest with everyone you’re working with.
How eSUB Can Help
eSUB is a cloud-based project management platform built especially for subcontractors. It seamlessly integrates with leading construction software systems so you can easily switch from your current document process to a cloud-based system to upgrade your construction project management process.
eSUB organizes all of your project information in one place, allows for smooth collaboration, and streamlines communication through its intuitive interface. It also works on your mobile, so you can track projects on the go—no matter where or when—and stay up-to-date.
This is a guest post from Jason O’Leary of Surety Bonds Direct. Jason brings 15 years of deep technology, product development, and marketing experience to Surety Bonds Direct. He has been leveraging Agile practices for well over a decade and is versed in various Lean practices as well. Jason has worked on substantial and complex systems dealing with secure information ranging from payroll & employee systems to e-commerce, to travel-reservation APIs.