Concrete Polishing: What You Need To Know
Certain areas of a structure or building may be pulling the property manager in multiple directions, like how to handle the floor. For example, you may have a floor that needs to have the proper strength to handle heavy item movement. Naturally, concrete sounds like the ideal fit. However, this same area is also going to get a lot of foot traffic. As a result, you don’t want to run the risk of the surface getting worn out. A good balance here is utilizing concrete polishing. This is an ideal fit to provide an attractive glossy look while still retaining the best properties of concrete. So, here are the fundamentals of polished concrete and how exactly the process goes.
Table of Contents
Why Polished Concrete?
Before talking about your first concrete polishing machine, let’s discuss some of the key benefits of adopting this practice. For one thing, by grinding a concrete floor into a gloss finish, you minimize the future need for coatings and waxes. In addition, the gloss finish provides benefits like:
- -High durability
- -Impact resistance
- -Peeling resistance
- -Ease when it comes to cleaning
This makes polished concrete an ideal option when it comes to settings like office buildings, warehouses, and retail settings. Going back to our example earlier, you commonly see polished concrete floors in settings like superstores. In many cases, these need to deal with the wear and tear of impact and heavy foot traffic, while also being suitably presentable to the general public. Other settings where these may be required are manufacturing settings or showrooms. Here, they emulate polished stone while being a lot more functional.
The Versatility of Polished Concrete
Something else that works in favor of polished concrete is how versatile it is. Based on your upkeep capabilities and aesthetic needs, you can choose from a variety of different glosses to meet any application. To give you an idea of what you can do, you can choose a variety of colors, create patterns, or embed aggregates and objects into the concrete before you polish. We also can’t ignore the ease of care. Compared to other types of flooring, all you need to do with polished concrete is simply make sure you mop it and apply a cleaning product on occasion.
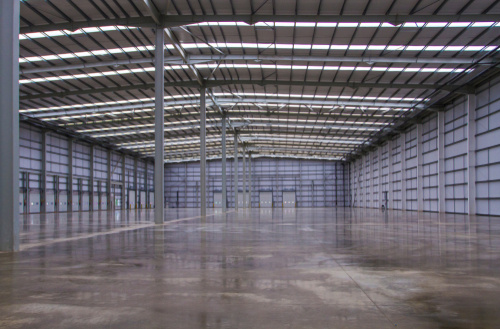
How the Process Works
How exactly does concrete polishing work? A good comparison is sanding down wood. A high-powered polishing machine uses discs that are similar to sandpaper to wear down the concrete until it meets the sheen and smoothness your client wants.
Discs
Let’s take a closer look at those discs, though. These discs generally begin with coarse segments of diamond that get bonded together in a metallic matrix. The goal here is to have something that can remove things like blemishes, stains, coatings, and pits from the floor. This can take multiple times, depending on the condition of the concrete.
When the abrasives are embedded in plastic or resin, that creates the discs that we’ve been discussing. A concrete polishing company will go over the floor in question with these discs, using grits that get finer and finer. This process is known as lapping and is done until you get the sheen you are looking for. It’s not unheard of for high-gloss finishes to use a grit of 1500 or even finer.
Sealer
Wearing down the concrete isn’t the only work that’s getting done with concrete polishing, though. At the same time, the professionals apply an internal impregnating sealer. This isn’t visible after it sinks into the concrete, but is an essential component of a proper polish. This sealer works to protect it internally, but also makes the concrete harder and denser. This means you no longer need a topical coating and save a lot of trouble in terms of upkeep. In some cases, for additional sheen, you may see an added polishing compound put on the surface. This also helps clean off the residue on the surface.
Two Main Methods of Concrete Polishing:
We mentioned the versatility of concrete polishing in terms of different steps that you can take. As an added note, there are also two main methods of concrete polishing: wet or dry. Each can be useful for certain circumstances, but dry is more common. With wet concrete polishing, water is used to cool off the abrasives and minimize dust. The main issue with wet polishing is cleaning it up. There’s a high amount of residue generated that the work crew then needs to collect and dispose of, keeping with environmental regulations. Dry polishing has the machine attached to a containment system that gathers most of the dust.
A lot of contractors have the best of both worlds, implementing both methods at different stages. For example, dry polishing sees more use at the beginning of the process, when more of the concrete is actually getting removed (generating dust). As it smooths more, and the abrasives get finer and finer, the crew then shifts to wet polishing.
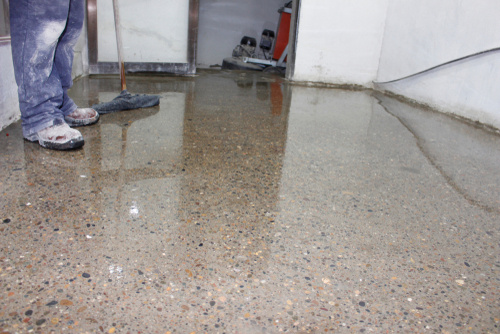
Business Potential with Polished Concrete
For many contractors, adding concrete floor polishing to your list of services is a great way to get business from clients that either may not need a full concrete installation or may have recently got one. This adds a lot of business potential, but of course, with that, comes a decision that needs to be made. Is the money that you get from this new option going to be enough to make up for the time and money that you spend to offer it in the first place?
Whether we’re talking about buying concrete polishing pads or onboarding your team, the best way to figure this out before you invest heavily in polishing concrete is by using project management software like eSUB. We have all the tools that you need to figure out exactly how much money you stand to make and have to spend in order to add polishing concrete to your suite of services as a contractor.