10 Tips to Increase Construction Productivity
The construction industry is one of the leaders in the world’s economy. In the U.S. alone, annual construction spending is estimated to be $1.2 billion. What is more, around 7% of the world’s population is working in the construction industry. Although there is a significant amount of money spent in this industry, studies have shown that construction productivity rates have dropped below those in the 1990s. The construction industry is now facing a productivity problem. Inefficiency in any project, whether it be big or small, causes a decrease in productivity levels. According to McKinsey Global Institute, if productivity in construction grew 2.8%, it is estimated the total world spending for the construction industry would increase by $1.6 trillion.
Many things that occur on the job site can lead to inefficiencies. Almost any change will hurt construction productivity rates. Changes to the scope of work or a schedule slip can lead to cost overruns. Nearly 98 percent of megaprojects suffer costs of 30% or more when there is a change to the project. The main reason for cost overruns, however, is low productivity.
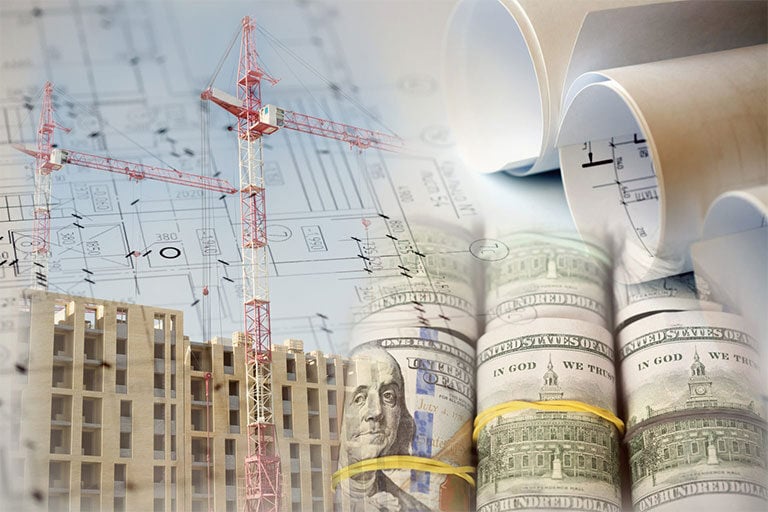
Productivity measures output per unit of input, such as labor, capital, or any other resource – and is typically calculated for the economy. Labor productivity may be further broken down by sector to examine trends in labor growth, wage levels, and technological improvement. Corporate profits and shareholder returns link to productivity growth directly.
When productivity increases:
— Construction projects finish on time
— Projects are more cost-efficient
— The overall project is more profitable
— Your company goes up in value and can bid more competitively
Table of Contents
10 Tips to Increase Construction Productivity
1. Utilize Technological Resources
By definition, labor productivity is directly affected by technological improvement. The productivity rates for the construction industry have dropped significantly behind every other sector. The construction industry is also spending less than 1% of its ten trillion-dollar revenue on information technology. Do you see a correlation? For the construction industry to catch up to its close relatives, it needs to adapt to today’s technology.
Through the use of project management software, companies can track their work more quickly than ever. Project management software can host construction documents such as Plans, Change Orders, RFIs or daily reports in one centralized location. Employees don’t need to waste time documenting things in multiple locations or better yet not documenting them at all then spending hours trying to figure out what previous work they completed. With hours saved on simple day-to-day tasks, project management software can help you free up time and increase your team’s productivity rates. In many cases up to 25%.
2. Construction Planning Based on Data
Construction projects develop at a swift pace, and, sometimes, it can be challenging to stay organized. However, lack of organization can ruin your project and ultimately affect your team’s productivity rates. Before you start any project, a plan needs to be in place. The more developed and prepared your plan is, the higher your productivity rates will be on any given project.
Improving your team’s use of data-driven strategies to drive planning efforts will increase productivity. One solution, BIM, Building Information Modeling, is a leading strategy among subcontractors to improve project delivery. BIM extracts the data from a project to create a 3D model of every structure before you start building. BIM is a useful tool in the planning process because it can predict job costs better than traditional methods because it knows how much building materials should cost. It can also give a better estimate of how long a project should take. When your team understands the workflow before they start working, it prevents mismanagement, resource misallocation, and, most importantly, boosts productivity.
3. Improve Communication
Even though you have created a fool-proof construction plan, this doesn’t mean that you have solved the problem completely. Poor communication is one of the causes of a lack of productivity in almost any industry. For construction, in particular, it can have a huge, negative impact on the final result. Consistent and effective communication between office and field and jobsite supervisors and workers will prevent mistakes and respect deadlines. Turning to a project management system designed around workflows can improve communication between team members by providing real-time updates to any changes on the job site.
Companies need not only to improve communication among employees but also communicate to employees the importance of productivity. Invest in training your supervisors and help them learn communication techniques. Provide suggestions to employees on how to improve productivity and set incentives to help them reach their goals.
4. Safety Before Anything
When it comes to construction safety, there’s always room for improvement. If you want to keep your construction productivity at the highest levels, you need to prevent injuries on the job site as much as possible. According to OHSA, one in every ten construction workers sustains an injured every year. And according to the National Safety Council, work-related injuries caused companies to lose a total of 104,000,000 production days in 2017.
Therefore, you need to invest in an effective safety program and train your employees about your company’s safety procedures and techniques. Raising awareness about safety will earn the trust of your employees, boost their confidence about the safety equipment they’re using, and drive your productivity levels even higher. Additionally, by keeping the accident rates low, you will avoid delays and extra expenses with the employees injured at work.
5. Use Prefabricated Building Systems
Recent trends show that many companies in the construction industry are using modular or prefabricated building systems. Prefabrication is the process of making buildings, or components of buildings, in a different location other than the job site itself. Construction companies will then transport these components to the jobsite and complete the set-up.
Prefabrication takes significantly less time to build compared to on-site construction. It takes less than half the time compared to traditional on-site installation. Prefabrication helps overcome weather delays or running into other trades at the jobsite site. Shorter construction times allow companies to take on more projects and spend less time on traditional construction activities. It will be easier for your company to focus on multiple projects at once. What does this mean? Improved productivity!
6. Invest in Training and Require More Job Experience
A company’s most valuable asset is its employees. Thus, if you want your teams to perform to their highest potential, you need to invest in them. Providing a sophisticated training program for your employees will make them feel more knowledgeable and more valuable to your company. Additionally, the tools and skills they learn during training will make them more efficient on the job site.
Now, with the high innovation pace, you must keep your employees up to date. They need to know how to use the latest technologies and be able to teach their teams as well. Hiring experienced managers to guide your employees through times of change is essential. Ultimately, when you have well-prepared employees, your productivity will overall increase.
7. Set Realistic Goals and Offer Recognition
Even if you offer various incentives to your workers to finish the project faster, you still need to set realistic goals. Evaluate the resources you have and establish realistic goals when it comes to project deadlines. You can leverage the field data collected in your project management platform from previously jobs to accurately set baselines. Your workers can be the best of the best, but they are still humans. When you set unrealistic goals and put too much pressure on your employees, they might make more mistakes because of the stress. Setting attainable goals encourage employees and boost productivity levels by showing workers they are cable of getting the job done.
There’s no better motivation for your employees than to feel that their work is appreciated. When you notice that they are excelling in their position, acknowledge their work, and present them as an example for the others. You can take things even further and offer periodical rewards and prizes. Incentives are the simplest method you can use to keep your employees motivated and increase your productivity.
8. Move Towards Shorter Contracts
Construction contracts are typically very lengthy and augmented with legal jargon. When general contractors and subs draft contracts with as much legal insulation as possible, it makes it difficult for team members to understand the outline of the project. Clear and concise contracts eliminate confusion and provide a playbook for workers performing the job to reference.
When team members are confused or not on the same page, they can make mistakes, and costly rework is required. To ensure your team stays productive, consider shortening the length of your contracts, and only include information that is valuable to the projects itself.
9. Organize Your Sites and Update Inventory
A construction site is usually a mess. However, this is one of the causes of low productivity. A construction site doesn’t need to be neat and tidy, but it should stay organized. When a construction site is littered with debris and extra material, accidents and equipment damage are more likely to occur. What is more, when employees can’t find their tools and materials, they will waste their time searching instead of working. In addition to keeping your site organized, you should know the exact inventory you’re keeping on-site.
By keeping an updated inventory, you will be able to order new materials when you discover that the stock will soon run short. Also, an updated list helps you forecast your purchases and investments for the following period. Keeping an inventory of your stock will help keep your site organized, eliminate waste, and keep your projects productive.
10. Delegate Tasks
You may have very skilled and smart people on your team, but most of the responsibilities are overloaded on the most efficient employees. On the contrary, you should split the tasks based on different people’s strengths. Each person has a particular skill, and you should use it to increase productivity. If you want fast results, learn to delegate smartly and make sure that people do what they know to do best.
The construction sector is one of the most competitive out there. Keeping up with the productivity rates of your competitors will not only help you win jobs but become a more fine-tuned and successful machine. Whether you implement new technology, expand your planning process, or establish better ways to communicate, your company’s operational and site productivity will improve.
If your teams are struggling with sharing construction project data, unable to get people in sync or spending too much time on unproductive work, eSUB might be able to help. Contact us today to schedule a demo.